Контроль качества литой арматуры с использованием магнитной памяти металла
д.т.н., профессор Дубов А.А.
В настоящее время существует проблема определения дефектов литья на корпусах арматуры неразрушающими методами контроля. В статье представлен опыт комплексного контроля методом магнитной памяти металла в сочетании с ультразвуком дефектов литья в корпусах арматуры высокого давления, установленной на компрессорных станциях и устройствах газодобычи ОАО "Газпром". Даны рекомендации по применению комплексного контроля дефектов литья как на заводах-изготовителях арматуры, так и в условиях ее эксплуатации.
Металлургические дефекты, как известно, создают в локальных зонах корпусов чугунной и стальной арматуры высокий уровень остаточных напряжений (ОН). Контроль ОН на заводах-изготовителях арматуры, как правило, не выполняется. Определение дефектов литья в глубинных слоях металла корпусов с использованием ультразвукового контроля является проблемной задачей. Из-за сложной конфигурации дефектов литья внутри металла корпусов в настоящее время нет четких инструкций по выявлению дефектов с использованием ультразвукового контроля (УК).
Каждый раз индивидуально на каждой единице арматуры ультразвуковой контроль приходится выполнять в поисковом режиме (выбор частоты и угла наклона луча, выбор зоны контроля на поверхности корпуса).
В настоящее время оценка технического состояния запорно-регулирующей арматуры магистральных газопроводов выполняется в соответствии с СТО Газпром 2-4.1-406-2009, а фонтанной арматуры в соответствии с методикой ОАО "Оргэнергогаз". В обоих документах метод магнитной памяти металла (МПМ) включен для его применения в качестве экспресс-метода определения на поверхности корпусов арматуры зон концентрации напряжений, возникающих от дефектов литья в сочетании с рабочими нагрузками.
Как известно, применение метода МПМ не требует какой-либо подготовки поверхности. Контроль может выполняться как на отключенной арматуре, так при ее работе под нагрузкой, через слой краски и при этом используется естественная намагниченность металла. Основные методические рекомендации по применению метода МПМ приведены в учебном пособии [1].
При включении метода МПМ в указанные руководящие документы предполагалось, что метод МПМ должен быть первоочередным ко всем другим методам неразрушающего контроля (УК, толщинометрия, измерение твердости и др.), которые рекомендованы для оценки состояния арматуры. Однако, из-за того, что в руководящих документах нет четких указаний по порядку применения всех перечисленных методов НК и их назначению, взаимодополнению, на практике каждый метод НК применяется самостоятельно, без какой-либо связи между собой.
На рис.1 показан пример контроля корпуса шарового крана ГПА-1 ⌀400 КС-1 Екатеринского ЛПУ МГ ООО "Газпром трансгаз Саратов".
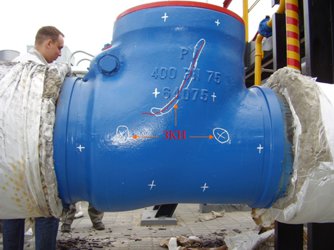
Отметки мелом в виде крестиков (+) указывают зоны контроля толщины и твердости металла корпуса с наружной поверхности, рекомендуемые инструкцией для данных методов НК. По результатам измерения толщины стенки и твердости в указанных зонах контроля отклонений этих параметров по сравнению с проектными не выявлено. Здесь же, на рис.1 указаны зоны магнитных аномалий, выявленные методом МПМ. Эти аномалии соответствуют зонам концентрации напряжений (ЗКН), возникновение которых, как правило, обусловлено дефектами литья и рабочими нагрузками.
В одной из зон, выявленных методом МПМ, после зачистки металла на этом корпусе была обнаружена протяженная трещина длиной ~250мм и глубиной не менее 5мм (по данным вихретокового контроля). Данный пример наглядно показывает методическую недоработку руководящих документов в рекомендациях по применению различных методов НК. Необходимо было выполнять измерение толщин и твердости, в первую очередь, в ЗКН, выявленных методом МПМ. Наш опыт показывает, как и в этом случае, в ЗКН значения твердости и толщин значительно отличаются от расчетных, особенно, если в этих зонах уже имеется развивающееся повреждение.
Здесь также необходимо отметить, что во всех ЗКН, выявленных методом МПМ, рекомендуется выполнять контроль ультразвуковым методом с целью определения наличия дефектов, их протяженности и глубины. Для определения наличия поверхностных трещин рекомендуется применять вихретоковый метод контроля и соответствующие приборы, не требующие зачистки поверхности арматуры.
Известно, что определение наличия и размеров дефектов в литых изделиях ультразвуковым методом на практике является сложной задачей. В сочетании с методом МПМ задача контроля дефектов литья в корпусах арматуры значительно упрощается. По результатам контроля методом МПМ представляется возможным с точностью до 1 мм указать место установки пьезопреобразователей УК и угол ввода луча.
Рассмотрим другой пример из практики контроля методом МПМ шарового крана ⌀700мм, выполненный специалистом ООО "Энергодиагностика" в Башмаковском ЛПУ МГ ООО "Газпром трансгаз Саратов".
На рис.2 приведена магнитограмма распределения градиента магнитного поля, зафиксированная при контроле вдоль периметра выходной (по ходу газа) части крана.
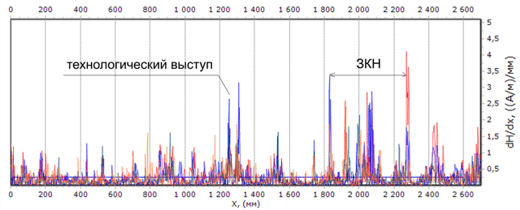
На рис.3 показан фрагмент выходной части этого крана с выявленными трещинами после зачистки поверхности металла в ЗКН.

На рис.4 показан фрагмент этой зоны после выборки металла с трещинами. Видно, что глубина и площадь выборок металла довольно значительные.
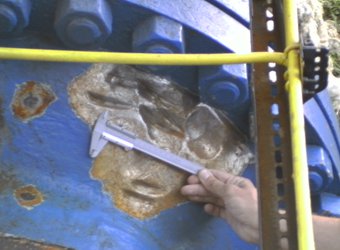
Опыт контроля шаровых кранов ⌀700мм с аналогичной конструкцией показывает, что ЗКН, выявляемые методом МПМ, и, соответственно, развивающиеся трещины в этих зонах от дефектов литья, в основном, расположены на выходной утолщенной части крана.
Здесь следует отметить, что не во всех ЗКН, выявляемых методом МПМ, размеры обнаруживаемых дефектов и их опасность развития до сквозных являются одинаковыми. Основная задача метода МПМ заключается в том, чтобы по результатам контроля выполнить классификацию ЗКН и выявленных дефектов по степени их опасности. Для этого должны быть разработаны количественные критерии для однотипных конструкций арматуры на основе практических данных контроля. Например, в результате контроля методом МПМ 18-и однотипных шаровых кранов ⌀700мм на трех КС ООО "Газпром трансгаз Саратов" было выявлено 101 ЗКН. Из них только приблизительно в 15-ти ЗКН имеются развивающиеся дефекты литья. При этом в сочетании с ультразвуковым методом из этих 15 ЗКН представляется возможным назвать 3-4 ЗКН, наиболее опасные для развития трещин на конкретных номерах кранов для периодического их контроля. Но для принятия такого решения должна быть разработана специальная комплексная методика контроля и соответствующий руководящий документ ОАО "Газпром".
Аналогичные проблемы выявлены при контроле корпусных деталей фонтанной арматуры. Как известно, давление газа внутри фонтанной арматуры достигает 200кГс/см2, и толщины стенок на этом типе арматуры значительно больше по сравнению с запорно-регулирующей арматурой на КС. При большей толщине стенок дефекты литья на фонтанной арматуре обнаруживались на глубине 20÷30мм и более при выполнении комплексного контроля методами МПМ и УК.
На основе значительного опыта контроля фонтанной арматуры, полученного в результате выполнения большого объема работ специалистами ООО "Энергодиагностика" совместно со специалистами ОАО "Оргэнергогаз" на предприятиях ООО "Ямбурггаздобыча", еще в 2000 году была разработана "Методика определения зон концентрации напряжений корпусных деталей фонтанной арматуры с использованием метода МПМ". Однако, при составлении руководящего документа ОАО "Газпром" не были учтены основные положения, имеющиеся в методике ООО "Энергодиагностика". В указанной методике имеются количественные критерии по оценке предельного состояния металла в ЗКН. В руководящем документе только есть рекомендация об использовании метода МПМ наряду с другими методами НК.
В заключении следует отметить следующее. Анализ повреждений корпусов литой арматуры показывает, что основной причиной является наличие дефектов литейного производства. Из-за сложной конфигурации дефектов литья в объеме металла корпусов на заводах-изготовителях арматуры существует проблема определения этих дефектов неразрушающими методами. В данной статье представлен опыт комплексного контроля (методом МПМ в сочетании с УК) корпусов литой арматуры, установленной на газопроводах высокого давления. В условиях, когда методом МПМ в режиме экспресс-контроля предварительно определяется наличие или отсутствие дефектов литья с указанием на наружной поверхности корпуса зоны расположения дефектов, эффективность выявления несплошностей в объеме металла ультразвуковым методом значительно повышается. Во многих случаях, когда известна ЗКН, определяемая методом МПМ на поверхности корпуса, предоставляется возможность определить несплошности литейного происхождения внутри металла ультразвуковым толщиномером.
Рекомендуется выполнять такой комплексный контроль дефектов литья в корпусах арматуры как на заводах-изготовителях, так и в условиях их эксплуатации.
При разработке практических методик предлагаемого комплексного НК литых корпусов арматуры необходимо учитывать степень опасности выявленных дефектов литья. Как показывает опыт контроля арматуры методом МПМ, одни дефекты литья могут создавать высокую концентрацию напряжений и, соответственно, вызывать развитие трещин вплоть до сквозных, а другие дефекты являются "спокойными" и не создают концентрацию напряжений. Основное назначение метода МПМ именно в том и заключается, чтобы сделать оценку уровня концентрации напряжений в выявленных ЗКН, используя количественные магнитомеханические параметры.
Литература
1. Дубов А.А., Дубов Ал.А., Колокольников С.М. Метод магнитной памяти металла и приборы контроля: Учебное пособие. М.: Издательский дом "Спектр", 2012. 395 с.