Контроль напряженно-деформированного состояния газопроводов при оценке их ресурса
д.т.н., профессор Дубов А.А.
В статье отмечена необходимость неразрушающего контроля напряженно-деформированного состояния магистральных газопроводов при их ремонте и продлении ресурса эксплуатации. Представлен опыт применения метода магнитной памяти металла и сканирующих устройств для решения указанной задачи. Приведены примеры определения зон стресс-коррозии на раннем этапе ее развития.
В настоящее время при капитальном ремонте магистральных газопроводов с их переизоляцией широко используется отбраковка труб с помощью сканеров-дефектоскопов (ультразвуковых, магнитных, вихретоковых). Как показала практика, все сканеры-дефектоскопы исполняют роль индикации дефектных зон. В дальнейшем, в этих зонах выполняется уточняющий контроль в "ручном" режиме с сортировкой по видам дефектов и их классификацией на допустимые и недопустимые в соответствии с "Инструкцией по оценке дефектов труб и соединительных деталей при ремонте и диагностировании магистральных газопроводов", утвержденной ОАО "Газпром" 18 ноября 2008 года.
Результаты контроля с помощью сканеров-дефектоскопов в отдельных случаях сравнивают с результатами внутритрубной диагностики, и на основе такого сравнения принимается решение о допуске газопроводов к переизоляции и дальнейшей эксплуатации.
Следует отметить существенный недостаток сложившегося подхода к обеспечению надежности магистральных газопроводов, бывших в эксплуатации, на дальнейший срок продления их ресурса (20-30 лет и более).
Этот недостаток заключается в том, что при таком подходе выявляются и устраняются недопустимые дефекты, развитые во время предыдущего срока эксплуатации газопроводов.
Развивающиеся дефекты в зонах максимальной концентрации напряжений, по своим размерам лежащие за пределами чувствительности традиционных методов НК, не выявляются и допускаются в дальнейшую эксплуатацию на длительный период времени.
Рассмотрим эту проблему на примере результатов контроля газопроводов с использованием метода магнитной памяти металла.
Метод МПМ выполняет при неразрушающем контроле одновременно две задачи.
Первая задача - выявление дефектных зон на внутренней и наружной поверхности трубы с их последующей классификацией, т.е. выполнение обычной задачи дефектоскопии.
Вторая задача - выполнение контроля напряженно-деформированного состояния металла трубы и сварных соединений с определением зон концентрации напряжений - источников всех видов повреждений на раннем этапе их развития.
Кроме того, метод МПМ не требует никаких подготовительных работ при выполнении контроля и отличается от других методов НК тем, что он указывает уровень концентрации напряжений, т.е. указывает степень опасности выявленных дефектов.
Исходя из указанных особенностей метода МПМ, сделаем анализ результатов контроля, представленных на рис.1.
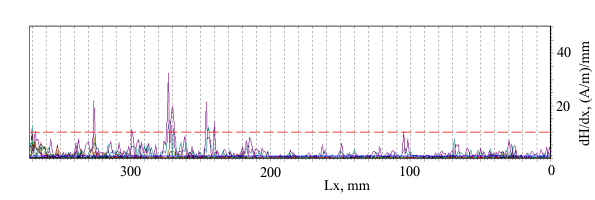
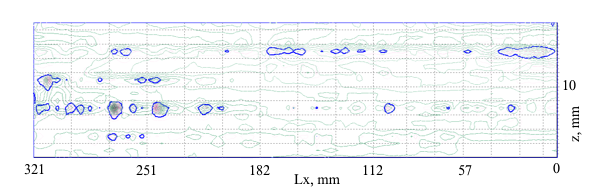
Из рисунка видно, что дефектные зоны со значением градиента поля (dH/dx) выше 10 (А/м)/мм, расположенные выше ограничивающей линии, соответствуют недопустимым дефектам по нормам отбраковки, согласно указанной выше "Инструкции...", а все дефектные зоны со значением градиента dH/dx<10 (А/м)/мм соответствуют допустимым дефектам.
Вот именно эти дефектные зоны со значением градиента поля ниже 10 (А/м)/мм, в которых идет процесс развития дефектов, остаются в дальнейшую эксплуатацию. При отбраковке труб на ремонтной базе значительную часть допустимых и недопустимых дефектов, расположенных на наружной поверхности трубы, можно убрать обычной зачисткой (шлифовкой). Однако, если такая операция по технологии, принятой на ремонтной базе, выполняется, то контроль на наличие или отсутствие дефектов металла с ранним развитием повреждений, в настоящее время не делается. Применение сканирующих устройств по методу МПМ позволило бы существенно дополнить существующую технологию отбраковки газопроводов на ремонтной базе или непосредственно при выполнении их переизоляции в полевых условиях.
Следует отметить, что отбраковка газопроводов, бывших в эксплуатации, на ремонтных площадках с использованием метода МПМ и специализированных сканирующих устройств успешно применялась в период с 2005 по 2009 год в ООО "Газпром трансгаз Томск". А на ремонтной базе ООО "Леноргэнергогаз" в 2007 году была проведена экспериментальная работа по проверке эффективности метода МПМ и сканирующих устройств по выявлению дефектных зон при сортировке труб в сравнении с ультразвуковым и вихретоковым методами НК. По результатам указанных работ предприятием ООО "Энергодиагностика" были составлены отчеты и представлены Заказчикам.
Сканер-дефектоскоп по методу магнитной памяти металла представляет собой сканирующее устройство (СУ) в виде двух скрепленных между собой колец, на которых установлены 32 феррозондовых датчика, совмещенных с колесиками, позволяющими оператору перемещать СУ вдоль трубопровода.
СУ используется в комплекте с сертифицированным прибором ИКН (измерителем концентрации напряжений), свидетельство Росстандарта RU.С.34.003.А №42683.
Скорость контроля трубы длиной 10÷11м составляет 3-5 мин с выдачей результатов о наиболее опасных дефектах в режиме реального времени с регистрацией магнитных сигналов от дефектов на экране и с записью в блок памяти прибора. Распечатка магнитограммы с расположением дефектных зон на часовой развертке трубы осуществляется в течение одного часа после выполнения контроля. Скорость контроля в одну смену не менее 30 труб с выдачей результатов.
Типоразмер труб ⌀530÷1420мм, и толщина стенки до 20мм и более. Обеспечивается контроль одновременно наружной и внутренней стенки трубы.
Вес СУ - 8 кг.
Чувствительность (выявляемость дефектов) датчиков СУ обеспечивает выявление всех дефектов, указанных в "Инструкции по оценке дефектов труб и соединительных деталей при ремонте и диагностировании магистральных газопроводов", утвержденной ОАО "Газпром" 18.11.2008. Морозоустойчивость СУ до -40 °С.
Подготовка поверхности трубы не требуется, контроль может выполняться без снятия изоляции. Используется естественная намагниченность трубы (магнитная память металла).
На рис.2 представлены фотографии, иллюстрирующие применение сканера на практике.
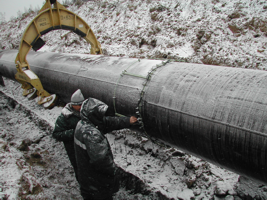
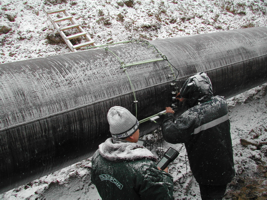
Рис.2. Применение сканера на практике.
При экспресс-контроле отдельных труб на ремонтной базе используются сканирующие устройства с частичным охватом трубы (рис.3).
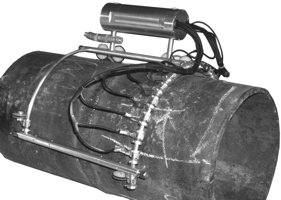
На отдельных трубах, где методом МПМ в режиме экспресс-контроля по "магнитным аномалиям" выявляются зоны концентрации напряжений с развивающимися дефектами, после снятия изоляции выполняется дополнительный контроль другими методами НК.
При таком комплексном контроле годными к дальнейшей эксплуатации принимаются трубы, на которых при контроле методом МПМ не были выявлены ЗКН с предельным значением градиента поля dHр/dx (Кпр), соответствующим начальному этапу развития повреждения, и не были выявлены недопустимые дефекты по ВСН 39-1.10-009-2002 другими методами НК.
Негодными к дальнейшей эксплуатации принимаются трубы, имеющие предельный градиент магнитного поля Кпр в ЗКН, различные дефекты (язвины на внутренней и наружной поверхности, расслоение металла, механические повреждения, гофры и др.) и утонение стенки в отдельных зонах на 10-20%. Часть труб, имеющих незначительные ЗКН и дефекты, утонение стенки менее 10%, признаются годными к повторному применению после их ремонта. Контроль методом магнитной памяти металла выполняется в соответствии с ГОСТ Р 52005-2003 и "Инструкцией по оценке дефектов труб и соединительных деталей при ремонте и диагностировании магистральных газопроводов", утвержденной ОАО "Газпром" 18.11.2008.
В настоящее время для контроля кольцевых сварных швов магистральных газопроводов, бывших в длительной эксплуатации, используются методы радиационного контроля (РК), ультразвуковой контроль (УК) и результаты внутритрубной диагностики (ВТД). В полевых условиях выполняется, как правило, выборочный контроль монтажных кольцевых швов. Заводские кольцевые швы практически не контролируются, так как считается, что они имеют более высокое качество по сравнению с монтажными швами.
Однако после длительной эксплуатации газопроводов при выполнении капитального ремонта и в процессе их переизоляции требуется выполнять выборочный неразрушающий контроль (НК) не только монтажных, но и отдельных заводских стыков. Особенно важно выполнять такой контроль на отводах, перемычках и везде, где не может использоваться ВТД. После длительного периода эксплуатации и производства других "вскрышных" работ, когда есть необходимость оставить старые трубы в эксплуатации на дальнейший длительный период, представляется необходимым обеспечить НК не только металла сварных соединений, но и зон термического влияния шва (ЗТВ), в которых наиболее вероятно развитие повреждений. Применение РК и УК для выполнения даже выборочного НК "старых" заводских и монтажных кольцевых сварных соединений является трудоемким, а для отдельных угловых тройниковых соединений (на отводах, перемычках и т.д.) практически невыполнимым.
В этих условиях предпочтительным является применение физического метода, позволяющего определять качество сварных соединений в режиме экспресс-контроля и без подготовки поверхности. К таким методам НК относится метод магнитной памяти металла (МПМ), который в настоящее время получает все большее распространение на практике при контроле кольцевых сварных соединений газопроводов. Используя естественную намагниченность металла, сложившуюся в процессе сварки, метод позволяет выполнять предварительную экспресс-сортировку сварных швов по принципу "удовлетворительно" и "неудовлетворительно".
По результатам такой предварительной сортировки определяются сварные соединения, которые необходимо дополнительно проконтролировать с применением РК или УК с указанием зон с максимальными дефектами.
Кроме того, как указывалось ранее, метод МПМ дает оценку степени опасности выявленных дефектов для развития повреждений и одновременно дает оценку напряженно-деформированного состояния (НДС) зон термического влияния сварных соединений газопроводов.
В 2008 году по договору с ООО "Газпром трансгаз Томск" по плану НИОКР предприятием ООО "Энергодиагностика" разработана "Методика контроля кольцевых сварных соединений магистральных газопроводов, бывших в эксплуатации, методом магнитной памяти металла". Методика согласована с Департаментом по транспортировке, подземному хранению и использованию газа.
Методика прошла широкую промышленную проверку, в первую очередь, в ООО "Газпром трансгаз Томск", и может быть рекомендована для ее применения на других предприятиях ОАО "Газпром" при выполнении капитальных ремонтов магистральных газопроводов.
Применение данной методики в сочетании с ультразвуковым методом повышает скорость и эффективность контроля кольцевых сварных соединений.
Особо необходимо остановиться на проблеме повреждений магистральных газопроводов по причине коррозии под напряжением (КРН). Известно, что наиболее часто эти повреждения развиваются в зонах повышенной концентрации остаточных напряжений (ОН), сформировавшихся при изготовлении трубопроводов. Одна из этих зон расположена на расстоянии ~150÷300 мм (в зависимости от диаметра трубы) в обе стороны от продольного сварного шва. Другим местом повышенных ОН является зона термического влияния кольцевых и продольных сварных соединений газопроводов. Проблема развития КРН в зонах с повышенной концентрацией напряжений известна, однако на практике в настоящее время контроль наличия (или отсутствия) этих зон и уровень концентрации напряжений в них до сих пор отсутствует.
Следует отметить, что необходимость неразрушающего контроля ОН и напряженно-деформированного состояния на трубопроводах различного технологического назначения (не только газопроводов) до последнего времени не находила должного отражения в нормативных документах эксплуатирующих организаций. Однако в последние годы это положение существенно изменилось.
В 2009 году Ростехрегулированием утвержден ГОСТ Р ИСО 9712-2009 "Контроль неразрушающий. Аттестация и сертификация персонала", которым введена в практику сертификация специалистов по новому виду НК "Контроль напряженно-деформированного состояния".
Ранее, в 2005 году Ростехрегулированием был введен в действие ГОСТ Р 52330-2005 "Контроль неразрушающий. Контроль напряженно-деформированного состояния объектов промышленности и транспорта. Общие требования". В том же 2005 году Президентом РОНКТД был утвержден документ "Система добровольной сертификации персонала в области неразрушающего контроля и диагностики", где также обозначен новый вид НК "Контроль напряжений".
В сентябре 2010 года в ОАО "НТЦ "Промышленная безопасность" утверждено "Положение об аттестации специалистов в области неразрушающего контроля напряженно-деформированного состояния". Среди методов НК НДС в указанном "Положении" метод МПМ представлен как один из эффективных методов, предназначенный для решения данной задачи.
В Положении об аттестации экспертов в области промышленной безопасности (СДА-12-2009), принятым Наблюдательным Советом решением от 20.07.2009 №30-БНС, также отмечена необходимость оценки НДС трубопроводов и технических устройств при их экспертизе.
Таким образом, в настоящее время имеются все предпосылки (а самое главное, практика требует) для организации НК НДС газопроводов (как вновь монтируемых, так и бывших в эксплуатации).
В этой связи, имеющийся более чем 25-летний опыт применения метода МПМ на практике для различного оборудования, в том числе и для магистральных газопроводов, позволяет заявить об его эффективности при решении указанной выше задачи НК НДС газопроводов при выполнении на них ремонтных работ.