Диагностика узлов и деталей бурильных установок нефтедобычи с использованием метода магнитной памяти металла
д.т.н. Дубов А.А., к.т.н. Дубов Ал.А., Собранин А.А.
Одной из причин происходящих повреждений деталей и узлов установок нефтедобычи является несовершенство применяемых методов неразрушающего контроля, как на заводах-изготовителях изделий (начиная с заготовок), так и в условиях эксплуатации.
В статье представлен опыт применения метода магнитной памяти металла при ранней диагностике повреждений новых и бывших в эксплуатации деталей установок нефтедобычи.
В настоящее время, на установках нефтедобычи периодически происходят повреждения отдельных наиболее нагруженных узлов и деталей, вследствие неудачного сочетания технологических дефектов изготовления с условиями эксплуатации.
Традиционные методы НК: рентген, ультразвук, вихретоковый метод, магнитопорошковый метод, цветная дефектоскопия, - направлены, как известно, на поиск и обнаружение явновыраженных дефектов, расположенных, преимущественно, на поверхности изделий [1].
Внутренние дефекты литья, различного рода неоднородности структуры, а также технологические дефекты изготовления (дефекты сварки, проката, гибки, термообработки и др.) из-за отсутствия на большинстве заводов 100% контроля качества изделий, а также из-за несовершенства применяемых методов НК, остаются в изделиях невыявленными.
Технологические дефеты изготовления и дефекты металлургические, как известно, создают в локальных зонах изделия высокий уровень остаточных напряжений (ОН). Контроль ОН на отдельных производствах изделий выполняется выборочно. При этом контролируется средний (объемный) уровень ОН, а локальные зоны ОН от внутренних дефектов металла, как правило, не контролируются и пропускаются. Кроме того, неизвестно где эти локальные зоны расположены и как их можно обнаружить?
На предприятиях, которые эксплуатируют поступившие изделия машиностроения, входной контроль обычными методами НК, как правило, не выполняется или выполняется выборочно, частично. Контроль ОН при входном контроле, как правило, не выполняется. По указанным причинам в первые же годы эксплуатации изделий под рабочей нагрузкой происходит их отбраковка». Технологические и металлургические дефекты, вызывая высокий уровень ОН в локальных зонах изделий при неблагоприятных сочетаниях с напряжениями от рабочей нагрузки вызывают ускоренное развитие повреждений.
В настоящее время все большее распространение на практике при решении задач НК в новых изделиях и определения в них локальных зон ОН получает метод магнитной памяти металла (МПМ), разработанный фирмой ООО "Энергодиагностика" (Москва). На метод МПМ имеются российские и международные стандарты [2, 3].
Согласно ГОСТ Р ИСО 24497-1-2009 "Контроль неразрушающий. Метод магнитной памяти металла. Термины и определения" метод МПМ - метод неразрушающего контроля, основанный на регистрации и анализе распределения собственных магнитных полей рассеяния (СМПР), возникающих в зонах концентрации напряжений (ЗКН)1) и структурной неоднородности изделий. При этом СМПР отображают необратимое изменение намагниченности в направлении действия максимальных напряжений от рабочих (внешних) нагрузок, а также стуктурную и технологическую наследственность изделий и сварных соединений после их изготовления и охлаждения в магнитном поле Земли.
1) Следует отличать традиционное понятие "концентратор напряжений" от материаловедческого понятия "концентрация напряжений", возникающая в зонах устойчивых полос скольжения дислокаций, обусловленных действием рабочих нагрузок.
Метод МПМ принципиально отличается от всех известных магнитных методов НК тем, что при его применении не требуется искусственное намагничивание изделия, а используется естественная намагниченность и последействие, которое проявляется в виде магнитной памяти металла к фактическим деформациям и структурным изменениям.
Метод МПМ выполняет при неразрушающем контроле одновременно две задачи.
Первая задача - выявление дефектных зон на внутренней и наружной поверхности изделия с их последующей классификацией, т.е. выполнение обычной задачи дефектоскопии.
Вторая задача - выполнение контроля напряженно-деформированного состояния металла изделия и сварных соединений с определением зон концентрации напряжений - источников всех видов повреждений на раннем этапе их развития.
Кроме того, метод МПМ не требует никаких подготовительных работ при выполнении контроля и отличается от других методов НК тем, что он указывает уровень концентрации напряжений, т.е. указывает степень опасности выявленных дефектов.
Рассмотрим далее возможности метода МПМ при диагностике отдельных узлов и деталей бурильных установок нефтедобычи.
На рис.1 приведена фотография трубного участка бурового ствола ("статора"). С двух сторон статора имеется внутренняя резьба. При эксплуатации этих статоров под нагрузкой в местах начала внутренней резьбы образуются кольцевые трещины.
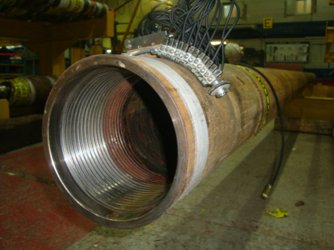
На производственной базе, занимающейся бурением нефтяных скважин с использованием метода МПМ, была проконтролирована партия новых статоров. Контроль выполнялся путем перемещения сканирующего устройства, подключенного к прибору типа ИКН (измеритель концентрации напряжения) вдоль наружных образующих трубы (рис.1). Если при такой схеме контроля в каком-то месте по длине трубы фиксировалось резкое локальное изменение магнитного поля, то в этом месте выполнялся дополнительный контроль вдоль периметра трубы. На рис.2 приведена магнитограмма, зафиксированная при контроле вдоль образующих с одной из сторон нового статора. Результаты контроля методом МПМ, представленные на рис.2, характеризуют удовлетворительное состояние нового статора.
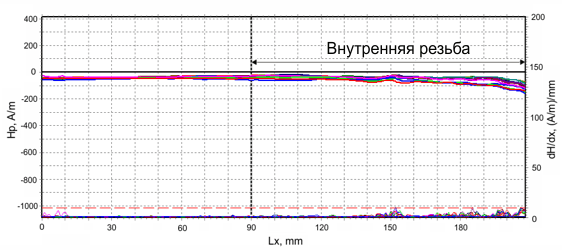
На рис. 3, а и рис. 3, б представлены результаты контроля другого нового статора с другим заводским номером. Схема контроля была аналогичной. Из рис.3 видно, что на новом статоре в зоне начала внутренней резьбы магнитное поле Hр и его градиентdH/dx имеют резкое локальное изменение. На круговой магнитограмме (рис.3, б) видно, что резкие локальные изменения поля имеют место в двух диаметрально противоположных зонах. Эти зоны по методике соответствуют зонам концентрации остаточных напряжений (ЗКН1 и ЗКН2), которые сформировались при изготовлении этого статора. На данном статоре при его эксплуатации под нагрузкой можно ожидать образования кольцевых трещин в ЗКН1 и ЗКН2. Именно в таких зонах статора во время эксплуатации или при профилактическом ремонте нередко обнаруживаются кольцевые трещины на первых витках внутренней резьбы.
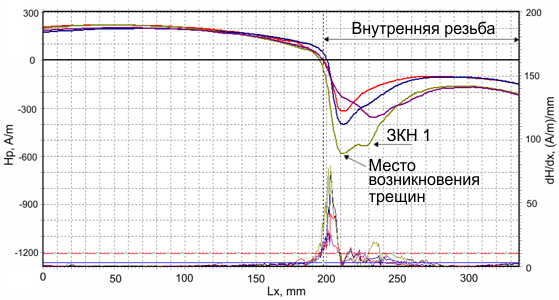
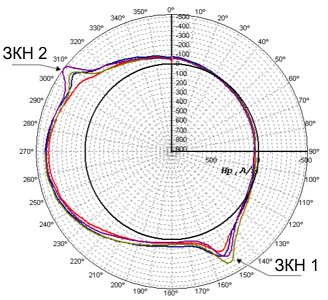
В подтверждение сказанному, на рис.4 приведены результаты контроля методом МПМ статора, бывшего в эксплуатации. Из рис.4 видно, что в месте образования трещины зафиксировано резкое локальное изменение магнитного поля и его градиента.
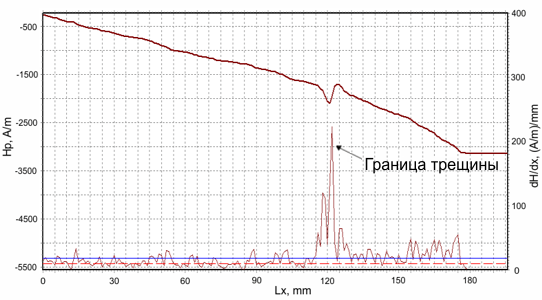
Рассмотрим далее результаты контроля методом МПМ рестрикторов (ограничителей), предназначенных для изменения проходного сечения и, соответственно, для изменения расхода движущейся среды внутри бурильной установки. На рис.5 представлен общий вид рестриктора, на корпусе которого стрелками указано направление контроля методом МПМ. На этом же корпусе показана трещина, образовавшаяся в процессе эксплуатации рестриктора.
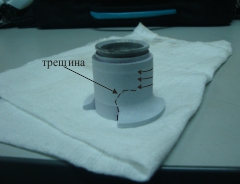
На рис.6 показана схема контроля СУ, встроенного в специальное приспособление. Путем прокрутки рестриктора на 360 градусов вокруг своей оси обеспечивается запись распределения собственного магнитного поля вдоль периметра рестриктора в сечениях, совпадающих с расположением датчиков СУ.
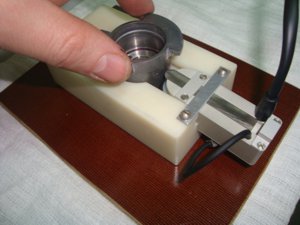
На рис.7 представлены результаты контроля методом МПМ новых рестрикторов. На рис.7, а показана магнитограмма, зафиксированная при контроле вдоль периметра в нижней (галтельной) части рестриктора модели № 6. ЗКН, зафиксированная на данном рестрикторе, совпадает с конструктивным концентратором напряжений - местом резкого локального изменения формы основания. На рис.7, б показана магнитограмма, зафиксированная при контроле в нижней части рестриктора модели № 7, которая характеризует удовлетворительное состояние.
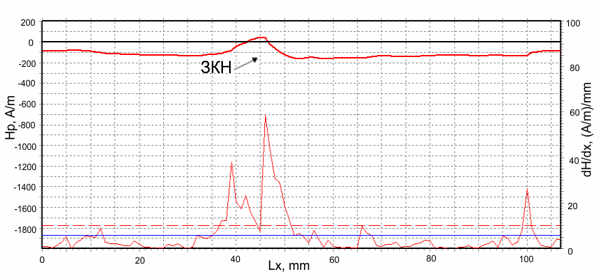
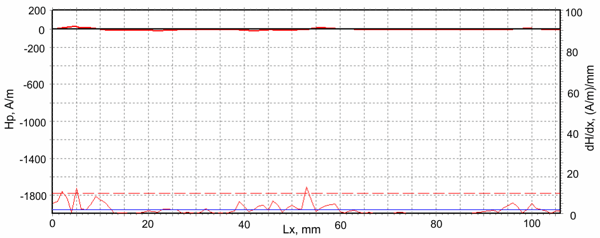
Аналогичные результаты контроля методом МПМ получены и на других изделиях установок нефтедобычи: ловильные головки насосно-компрессорных труб, валы электроцентробежных насосов и другие.
На основе результатов контроля методом МПМ вышеуказанных изделий бурильных установок и установок нефтедобычи можно сделать заключение о том, что в процессе эксплуатации ускоренное развитие повреждений происходит на изделиях, которые имеют в исходном состоянии локальные ЗКН, обусловленные металлургическими и технологическими дефектами изготовления.
Технологические и металлургические дефекты, расположенные в глубине металла изделий, применяемыми методами НК практически не выявляются. Если, например, поставить задачу с помощью ультразвукового контроля (УК) выполнить 100% контроль в ручном режиме и в поточном производстве изделий, то для оператора, в этом случае, должна быть составлена специальная инструкция для работы в поисковом режиме. Однако, даже в этом случае оператору нужно знать где и как поставить датчик УК, чтобы попытаться выявить внутренний дефект, расположенный на неизвестной глубине.
В автоматическом режиме такой контроль изделий в поточном режиме тем более невыполним.
Метод МПМ позволяет в режиме экспресс-контроля фиксировать магнитные аномалии, которые образуются на поверхности изделий в локальных зонах ОН, обусловленных внутренними дефектами металла. В зонах магнитных аномалий (зонах концентрации ОН) может быть дополнительно применен, например, ультразвуковой контроль. В этом случае, когда известна локальная зона ОН, оператор УК знает, где и как поставить датчик, эффективность комплексного НК изделия значительно повышается.
Заключение
Представленный в данной статье опыт применения технологии НК, основанной на использовании магнитной памяти металла, позволяет заявить о возможности осуществить 100% контроль, как новых, так и бывших в эксплуатации изделий, с целью выявления внутренних технологических и металлургических дефектов.
Контроль с использованием метода МПМ, не требующего никаких подготовительных операций, может быть автоматизирован при условии разработки специализированных сканирующих устройств, учитывающих конструктивные особенности изделия.
Литература
1. Неразрушающий контроль и диагностика: Справочник / Под редакцией академика РАН Клюева В.В. М.: Машиностроение, 1995. 487 с.
2. Власов В.Т., Дубов А.А. Физические основы метода магнитной памяти металла. М.: ЗАО "Тиссо", 2004. 424 с.
3. Дубов А.А., Дубов Ал.А., Колокольников С.М. Метод магнитной памяти металла и приборы контроля: Учебное пособие. М.: Издательский дом "Спектр", 2012. 395 с.