Определение локальных зон концентрации напряжений в изделиях машиностроения - недостающее звено в системе неразрушающего контроля
д.т.н., профессор Дубов А.А.
Известно, что основными источниками повреждений при эксплуатации изделий машиностроения являются локальные зоны концентрации напряжений (ЗКН), которые образуются под действием рабочих нагрузок в первую очередь на дефектах металлургического и технологического происхождения.
Металлургические и технологические дефекты изготовления, как известно, создают в локальных зонах изделия высокий уровень остаточных напряжений (ОН). Контроль ОН на отдельных производствах изделий выполняется выборочно. При этом контролируется средний (объемный) уровень ОН, а локальные зоны ОН от внутренних дефектов металла, как правило, не контролируются и пропускаются. Кроме того, неизвестно, где эти локальные зоны расположены и как их можно обнаружить?
Контроль ОН при входном контроле, как правило, не выполняется. По указанным причинам в первые же годы эксплуатации изделий под рабочей нагрузкой происходит их "отбраковка". Технологические и металлургические дефекты, вызывая высокий уровень ОН в локальных зонах изделий при неблагоприятных сочетаниях с напряжениями от рабочей нагрузки, вызывают ускоренное развитие повреждений.
Традиционные методы НК: рентген, ультразвук, вихретоковый метод, магнитопорошковая, цветная дефектоскопия, направлены, как известно, на поиск и обнаружение явно выраженных дефектов, расположенных, преимущественно, на поверхности изделий. Внутренние дефекты литья, различного рода неоднородности структуры, а также технологические дефекты изготовления (дефекты сварки, проката, гибки, термообработки и др.) из-за отсутствия на большинстве заводов 100% контроля качества изделий, а также из-за несовершенства применяемых методов НК, остаются в изделиях не выявленными. При этом сами нормы отбраковки применяемых методов НК на заводах-изготовителях изделий направлены на выявление дефектов с размерами, во много раз превышающими размеры металлургических дефектов. Например, по нормам ультразвукового контроля аустенитных труб допустимые дефекты имеют размеры, не превышающие длину 25 мм, раскрытие и глубину - 0,3 мм. Как показывает практика, металлургические дефекты с меньшими размерами, попадая под действие рабочих нагрузок, являются основными источниками эксплуатационных повреждений. В условиях эксплуатации изделий практически все методы НК также направлены на поиск различного вида несплошностей, размеры которых значительно превышают размеры дефектов, вызывающих развитие повреждений.
Таким образом, приходится констатировать, что отсутствие контроля ОН с целью определения концентрации напряжений на дефектах структуры изделий как на заводах-изготовителях, так и в эксплуатации, является недостающим звеном в системе НК изделий, что значительно снижает их надежность.
На рис.1 показана схема организации НК изделий машиностроения, сложившаяся в настоящее время как на заводах-изготовителях, так и в эксплуатации. Из рис.1 видно, что контроль изделий заключается в обычной дефектоскопии без оценки уровня концентрации напряжений на явных дефектах (несплошностях) и неявных (дефектах структуры). Пунктирной линией на рис.1 выделено недостающее звено в системе НК.
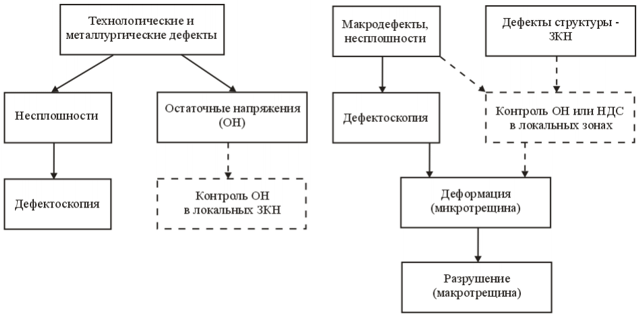
Следует отметить, что в настоящее время, когда в большинстве отраслей промышленности оборудование и конструкции достигли морального и физического износа, а материальных средств недостаточно для массовой их замены, значение неразрушающего контроля и технической диагностики становится все более актуальным. В этих условиях повышается роль экспресс-методов НК с целью обеспечения 100% обследования оборудования и выявления локальных ЗКН, в которых следует ожидать развитие повреждений при дальнейшей эксплуатации различных технических устройств.
В 2008 году введен в действие национальный стандарт ГОСТ Р 53006-2008 "Оценка ресурса потенциально опасных объектов на основе экспресс-методов. Общие требования".
К экспресс-методам отнесены пассивные методы НК, использующие внутреннюю энергию металла конструкций:
- метод акустической эмиссии (АЭ);
- метод магнитной памяти металла (МПМ);
- тепловой контроль.
Эти методы получили в настоящее время наибольшее распространение на практике для ранней диагностики повреждений оборудования и конструкций. Принципиальным отличием такого подхода к оценке ресурса является выполнение 100% обследования ОК с выявлением всех потенциально опасных зон концентрации напряжений (ЗКН) - источников возникновения повреждений при эксплуатации оборудования.
В новом национальном стандарте ГОСТ Р 53006-2008 отражены также следующие основные положения:
- в качестве основных критериев предельного состояния металла предлагается использовать фактические энергетические характеристики, которые можно определить методами МПМ, АЭ и тепловым методом;
- предложена структурная схема определения остаточного ресурса с акцентом на современные экспресс-методы технической диагностики;
- поверочные расчеты на прочность с оценкой остаточного ресурса предлагается выполнять для ЗКН, остающихся в эксплуатации, с учетом фактических структурно-механических свойств металла, выявленных при обследовании;
- учтены рекомендации национального стандарта ГОСТ Р 52330-2005 "Контроль неразрушающий. Контроль напряженно-деформированного состояния объектов промышленности и транспорта. Общие требования".
При реализации стандарта ГОСТ Р 53006-2008 представляется возможным в большинстве случаев без выполнения сложных поверочных расчетов на прочность делать экспертную оценку ресурса на основе комплексного обследования оборудования и назначать срок безопасной эксплуатации. Для конкретного оборудования возможна разработка более конкретной методики оценки ресурса с учетом специфических особенностей и требований, существующих в данной отрасли промышленности.
Все большее распространение на практике при решении задачи определения локальных ЗКН в новых и находящихся в эксплуатации изделиях получает метод магнитной памяти металла (МПМ), разработанный фирмой ООО "Энергодиагностика" (Москва). На метод МПМ имеются российские и международные стандарты.
Согласно ГОСТ Р ИСО 24497-1-2009 "Контроль неразрушающий. Метод магнитной памяти металла. Термины и определения" метод МПМ - метод неразрушающего контроля, основанный на регистрации и анализе распределения собственных магнитных полей рассеяния (СМПР), возникающих в зонах концентрации напряжений (ЗКН)1 и структурной неоднородности изделий. При этом СМПР отображают необратимое изменение намагниченности в направлении действия максимальных напряжений от рабочих (внешних) нагрузок, а также структурную и технологическую наследственность изделий и сварных соединений после их изготовления и охлаждения в магнитном поле Земли.
1)Следует отличать традиционное понятие "концентратор напряжений" от материаловедческого понятия "концентрация напряжений", возникающая на дефектах структуры и в зонах устойчивых полос скольжения дислокаций, обусловленных действием рабочих нагрузок.
Метод МПМ принципиально отличается от всех известных магнитных методов НК тем, что при его применении не требуется искусственное намагничивание изделия, а используется естественная намагниченность и последействие, которое проявляется в виде магнитной памяти металла к фактическим деформациям и структурным изменениям.
Метод МПМ не требует никаких подготовительных работ при выполнении контроля и отличается от других методов НК тем, что он указывает уровень концентрации напряжений, т.е. указывает степень опасности выявленных дефектов.
Рассмотрим далее возможности метода МПМ при диагностике новых изделий и бывших в эксплуатации с целью определения локальных ЗКН - источников развития повреждений.
На рис.2 представлены результаты контроля нового прутка ⌀22 мм (Ст.05Х16Н4Д2БТ13), из которого изготавливается вал электроцентробежного насоса (ЭЦН), выполненного на производственной базе ООО "ПК Борец" (г. Лебедянь).
На рис.2, а показана магнитограмма распределения нормальной составляющей собственного магнитного поля рассеяния H и его градиента dH/dх, зафиксированная в зоне концентрации напряжений (ЗКН) при сканировании датчиком прибора вдоль одной из образующих прутка №2204. На рис.2, б показано структурное состояние металла прутка №2204 в сечении, совпадающем с ЗКН. Цифрами указаны значе-ния микротвердости вдоль линии металлургического дефекта и вне его.
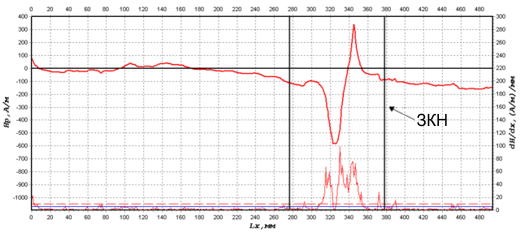
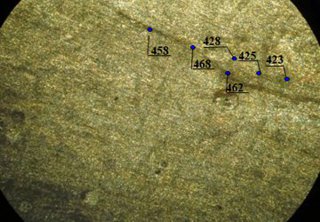
Рис.2. Результаты контроля прутка ⌀22 мм (Ст.05Х16Н4Д2Б-Т13), из которого изготавливается вал ЭЦН, выполненного на производственной базе ООО "ПК Борец", Лебедянь: а - магнитограмма распределения нормальной составляющей поля H и его градиента dH/dх, зафиксированная в зоне концентрации напряжений (ЗКН) при сканировании вдоль одной из образующих прутка №2204; б - структурное состояние металла прутка № 2204 в сечении, совпадающем с ЗКН. Цифрами указаны значения микротвердости вдоль линии металлургического дефекта и вне его.
На рис.3 представлены результаты контроля методом МПМ лопасти новой гидротурбины. На рис.3, а показано распределение магнитного поля H и его градиента dH/dх, зафиксированное при контроле вдоль наружной поверхности лопасти. На нижней части магнитограммы отмечена ЗКН, характеризуемая локальными изменениями градиента поля. На рис.3, б показаны дефекты литья, обнаруженные в глубине металла после разреза лопасти напротив ЗКН, зафиксированной методом МПМ на наружной поверхности.
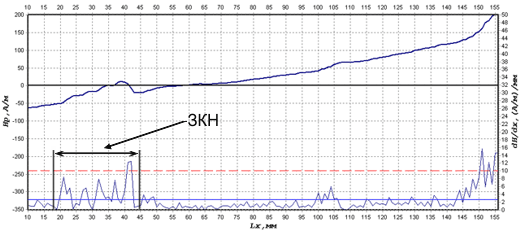
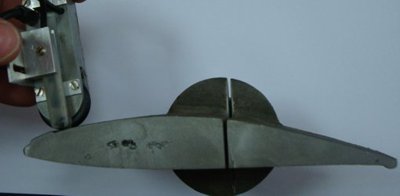
Рис.3. Результаты контроля методом МПМ лопасти новой гидротурбины: а - распределение магнитного поля H и его градиента dH/dх, зафиксированное при контроле вдоль наружной поверхности лопасти; б - дефекты литья, обнаруженные в ЗКН после разреза лопасти.
На рис.4 представлены результаты контроля методом МПМ трубы ⌀42х7 мм из стали 10Х13Г12БС2Н2Д2, вырезанной из нового ширмового пароперегревателя энергетического котла. На рис.4, а показана магнитограмма распределения собственного магнитного поля dH и его градиента dH/dх, зафиксированная в ЗКН на одной из образующих трубы. Несмотря на то, что данная труба изготовлена из нержавеющей стали, которая в исходном состоянии (после изготовления) должна быть практически немагнитной, однако из-за допущенных нарушений в технологии ее изготовления, в локальной зоне образовалась ферритная фаза, зафиксированная при контроле методом МПМ в виде магнитной аномалии. На рис.4, б показаны трещины, обнаруженные на внутренней поверхности образца трубы, вырезанного из зоны магнитной аномалии, соответствующей ЗКН.
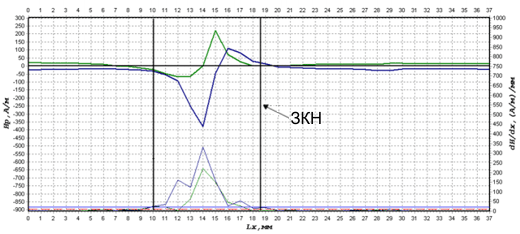
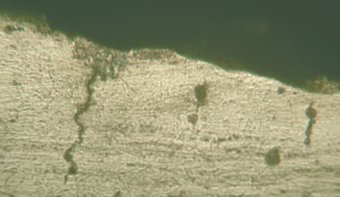
Рис.4. Результаты контроля трубы 42х7 из стали 10Х13Г12БС2Н2Д2, вырезанной из нового ширмового пароперегревателя энергетического котла: а - магнитограмма распределения собственного магнитного поля H и его градиента dH/dх, зафиксированная в зоне концентрации напряжений (ЗКН) на одной из образующих трубы; б - трещины, обнаруженные на внутренней поверхности образца трубы, вырезанного из ЗКН, выявленной методом МПМ.
Представленные на рис.2, 3 и 4 примеры из практики применения метода МПМ на новых изделиях различных производств убедительно показывают общие недостатки в организации НК на заводах-изготовителях. Все указанные изделия проходили через систему НК, существующую в настоящее время на заводах. Однако, как отмечалось выше, в настоящее время на большинстве заводов-изготовителей отсутствует контроль по выявлению дефектов металла, лежащих за нормированными пределами чувствительности применяемых методов и средств контроля. Применение метода МПМ, который проявляет дефекты металлургического и технологического производства в виде магнитных аномалий, соответствующих локальным зонам концентрации напряжений, позволило бы обеспечить 100% контроль изделий даже в поточном производстве.
При эксплуатации изделий машиностроения основными источниками развития повреждений также являются локальные ЗКН, места образования которых практически невозможно предсказать расчетными методами. С использованием метода МПМ представляется уникальная возможность путем выполнения 100% контроля различных узлов оборудования на раннем этапе выявить локальные зоны с максимальной концентрацией напряжений.
Для классификации магнитных аномалий, характеризующих ЗКН по степени их опасности в соответствии с методикой, изложенной в [1], делается сравнение всех магнитных аномалий, выявленных на данном узле по значению градиента поля dH/dх.
Для однотипных узлов оборудования на основе лабораторных и промышленных исследований определяется предельное значение градиента поля, при котором образуется микротрещина и начинается развитие повреждения.
В соответствии с определениями, представленными в работе [2], физический смысл магнитного параметра dH/dх заключается в том, что он отображает концентрацию (или плотность) магнитной энергии в объеме изделия, обусловленной плотностью энергии деформации.
На рис.5 представлены результаты контроля обода диска ступени паровой турбины 120 МВт. На рис.5, а показана магнитограмма, зафиксированная на наружной поверхности обода диска. В верхней части магнитограммы показано распределение тангенциальной 2 и нормальной 3 составляющих собственного магнитного поля H, а в нижней части магнитограммы - распределение градиента поля от указанных составляющих. Максимальное значение градиента поля 55 (А/м)/мм (или 55х103А/м2) примерно оказалось равным предельному значению для данного диска турбины, и поэтому в данном случае был сделан дополнительный контроль ультразвуком. При этом установка преобразователя прибора УК на диске корректировалась по месту расположения максимального значения градиента поля. При выполнении УК в ЗКН на внутренней поверхности паза была зафиксирована несплошность. После вырезки участка диска на внутренней поверхности паза была обнаружена трещина глубиной 2 мм и протяженностью 20 мм (см. рис.5, б и рис.5, в).
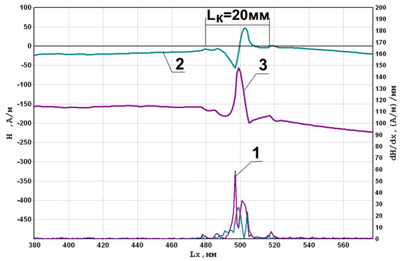
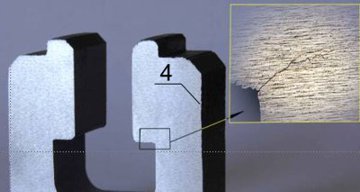
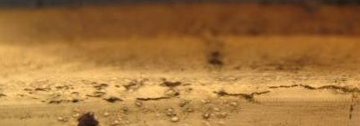
Рис.5. Результаты контроля обода диска ступени паровой турбины 120 МВт: а - фрагмент магнитограммы, зафиксированный на наружной поверхности обода диска со смещением вверх примерно на 45 градусов от расположения трещины на внутренней поверхности диска; б - место выявленной трещины глубиной ~2 мм; в - расположение трещины вдоль внутренней поверхности обода диска длиной ~20 мм (lк); 1 - максимальное значение градиента dH/dх; 2 - распределение тангенциальной составляющей поля H; 3 - распределение нормальной составляющей поля H; 4 - зона контроля методом МПМ с наружной стороны диска до вырезки фрагмента.
Здесь следует отметить, что в настоящее время, согласно действующей инструкции [3], ультразвуковой контроль дисков турбин с Т-образной посадкой лопаток на предмет выявления трещин в пазах выполняется с использованием специально изготовленных образцов, а сам контроль является сложной практической задачей. При выполнении УК обода диска в комплексе с методом МПМ вместо стандартного образца можно использовать способ сравнения сигналов УК в ЗКН, выявленной предварительно методом МПМ, и вне этой зоны. В этих условиях стандартные образцы не требуются, а ультразвуковой контроль может выполнять специалист средней квалификации.
Рассмотренный пример применения метода МПМ для выявления локальной ЗКН на раннем этапе развития повреждения наглядно показывает важность и эффективность его применения в комплексе с другими методами НК. Опыт применения метода МПМ на различном оборудовании, находящимся в длительной эксплуатации в различных отраслях промышленности, показывает, что только 5-10% общего объема металла достигает предельного состояния (физического предела прочности) и выходит на развитие повреждений. К сожалению, расчетными методами определить эти локальные ЗКН – источники развития повреждений, практически невозможно. С использованием методов ранней диагностики (метод МПМ, АЭ) такая задача может быть решена.
При анализе механизма разрушений изделий наиболее ценным является определение размеров локальных областей (объем, площадь, длина), при которых наступает предельное состояние металла и самого изделия. Именно эта сложная задача, которая до сих пор была предметом изучения в механике разрушений на образцах, с использованием метода МПМ решается непосредственно на оборудовании при диагностике состояния различных узлов.
Литература
1. Дубов А.А., Дубов Ал.А., Колокольников С.М. Метод магнитной памяти металла и приборы контроля: Учебное пособие. М.: ЗАО "Тиссо", 2008. 364с.
2. Власов В.Т., Дубов А.А. Физическая теория процесса "деформация-разрушение". Часть I. Физические критерии предельных состояний металла. М.: ЗАО "Тиссо", 2007. 517с.
3. Инструкция по продлению срока эксплуатации паровых турбин сверхпаркового ресурса. М.: ЦПТИ ОРГРЭС, 2004. 170с.