Диагностика гибов котельных и паропроводных труб
Одной из сложных проблем энергетики является обеспечение надежности гибов необогреваемых труб котлов и паропроводов. Несмотря на большое количество исследований и мероприятий, выполненных в масштабе отрасли "Электроэнергетика" с целью повышения надежности гибов, желаемые результаты до сих пор не достигнуты и гибы необогреваемых труб котлов продолжают оставаться аварийным узлом. Разработана методика раннего обнаружения повреждений гибов с использованием эффекта магнитной памяти металла. Существующие методы неразрушающего контроля (УЗК, МПД), которые широко применяются в энергетике, направлены на поиск и обнаружение уже развитых дефектов и различного рода трещин в металле оборудования, что является недостаточным, если рассматривать проблему обеспечения надежности гибов трубопроводов с точки зрения обеспечения безопасности обслуживающего персонала.
Вместе с тем известно, что основным источником разрушений гибов является концентрация механических напряжений, обусловленная действием рабочих нагрузок. Как правило, повреждаются гибы, работающие в условиях дополнительных (не расчетных) напряжений.
Из теории прочности и механики разрушений, известно, что наиболее неблагоприятным для развития повреждений оборудования является такое сочетание нагрузок, при котором металл локально находится под воздействием максимальных растягивающих напряжений. При этом зарождение трещин происходит по плоскостям, перпендикулярным максимальным растягивающим напряжениям. Многолетний опыт исследования магнитных полей на котельных и паропроводных трубах выявил наличие устойчивых линий смены знака нормальной составляющей напряженности магнитного поля Hр в зонах развивающихся повреждений металла. Именно этот диагностический параметр (линия Hр=0) был положен в основу методики контроля гибов. В более поздних исследованиях установлено, что в общем случае линия смены знака градиента поля соответствует линии максимальных напряжений от деформации сдвига. Интерпретация этого диагностического магнитного параметра, как линии главных напряжений, возникающей на поверхности труб под действием рабочих нагрузок, дана в специальной работе. Очевидно, что совпадение линий Hр=0 с растянутой или нейтральной зонами гиба трубы является наиболее опасным для его надежности.
Рассмотрим на примере контроля одного из гибов пароперепускных труб турбины ПТ-60 ст.№3 Дягилевской ТЭЦ (гиб №10, ст.15X1МФ, ⌀273х32 мм).
Контроль был выполнен с использованием двухканального датчика прибора ИКН-1М-4 вдоль растянутой стороны гиба. На рис.1,а приведена эпюра распределения поля Hр, зафиксированная в двухканальном режиме. Как видно из рис.1,а, зона концентрации напряжений (КН) характеризуется резким скачкообразным изменением поля Hр. Следует отметить, что сканирование вдоль растянутой зоны гиба выполнялось с базовым расстоянием между феррозондовыми датчиками, равным 20 мм. При этом резкое изменение поля Hр было зафиксировано в основном по одному каналу измерений. Затем в сечении гиба, где было зафиксировано резкое изменение поля Hр, был выполнен контроль вдоль периметра гиба.
На рис.1,б показано распределение поля Hр, зафиксированное вдоль периметра гиба (сечение А-А). Расстояние между феррозондовыми датчиками было также 20 мм. Из рис.1,б видно, что по одному из каналов зафиксировано значительное изменение величины и знака поля Hр, по другому каналу - изменение поля Hр менее значительное по величине и без изменения знака.
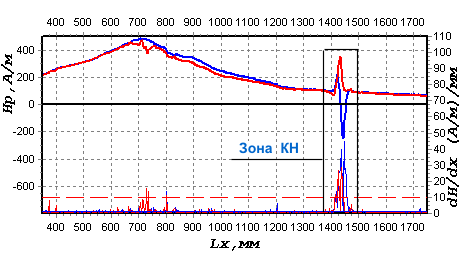
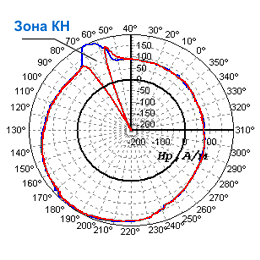
На рис.2,а показана зона КН, выявленная на гибе №10 вблизи растянутой стороны. Зона КН представляет собой пятно в виде эллипса с размерами 70х35 мм, т.е. кратному толщине стенки (32 мм). Пятно ограничено линией смены знака поля Hр (линией Hр=0). На рис.2,б показан фрагмент, иллюстрирующий защемление гиба №10 (с зоной КН) с трубой промотбора этой же турбины №3. Очевидно, что именно защемление гиба №10 при его температурной компенсации явилось причиной образования зоны КН.
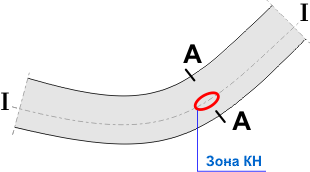
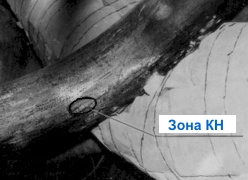
На рис.3 приведена структура металла, полученная с реплики, взятой из зоны КН (по линии Hр=0) на гибе №10. Как видно из рис.3, на данном гибе в зоне КН в структуре металла выявлены трещины с расстоянием между ними примерно 0,1 мм. Таким образом, гиб № 10 находился в состоянии предразрушения.
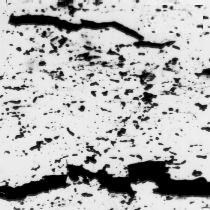
Представленная методика контроля гибов была согласованна с Главтехуправлением Минэнерго 25.02.1991г. и с Госгортехнадзором РФ 26.02.1993г., прошла промышленное опробование на ряде электростанций России и в других странах. Накоплен значительный положительный опыт, свидетельствующий об эффективности контроля гибов с использованием метода МПМ в сочетании с УЗК и с анализом структуры металла, полученной с реплик, взятых из зон КН. С учетом этого опыта в 2002 году данная методика была дополнена и переработана.