Контроль проволоки и канатов
Представленная ниже технология контроля может быть распространена на все виды сварочной и пружинистой проволоки.
Для обеспечения монтажа, ремонта и эксплуатации деталей, установленных в бурильных скважинах добычи газа и нефти, используется стальная проволока ⌀2,0 и ⌀2,6. Проволока изготавливается из стали 40-70 в соответствии с ГОСТ 9389-75, ГОСТ 1050-88, ГОСТ 14959-79, ГОСТ 1435-90.
В процессе эксплуатации и ремонта происходят повреждения проволоки, вызывающие большие материальные потери. С целью предотвращения повреждений проволоки необходима разработка и внедрение неразрушающих методов контроля, позволяющих своевременно выявить зоны концентрации напряжений (ЗКН). ЗКН, являющиеся источниками развития повреждений, могут быть как на новой проволоке, так и на проволоке, бывшей в эксплуатации.
На основании анализа результатов экспериментальных исследований, выполненных специалистами ООО "Энергодиагностика" на проволоке ⌀2,0 и ⌀2,6 с использованием метода магнитной памяти металла, были сделаны следующие выводы:
- Выявлена возможность использования метода МПМ для контроля качества проволоки, как новой, так и бывшей в эксплуатации.
- Контроль может осуществляться на производственной базе при перемотке проволоки с катушки на катушку и непосредственно на бурильной установке при подъеме или опускании оборудования.
- Выявлены количественные критерии предельного состояния металла проволоки разного типоразмера. Данные критерии необходимо уточнять в ходе промышленного внедрения метода МПМ и соответствующих приборов.
- Установлено, что метод МПМ и приборы типа ИКН-4М-16 позволяют выявлять ЗКН и зоны развивающихся повреждений на поверхности проволоки с точностью до 1 мм.
Основная задача метода МПМ - определение ЗКН - зон аномального распределения магнитных полей рассеяния на поверхности контролируемой проволоки. Затем, с использованием специализированной программы "ММП-Система", проводится сортировка проволоки по степени ее предрасположенности к повреждению в ЗКН. Отбраковка и сортировка проволоки может выполняться непосредственно при контроле, по значениям Кин, соответствующим предельному состоянию металла проволоки перед образованием трещин. Значение Кин, соответствующее предельному состоянию металла, определяется экспериментальными исследованиями для каждого типоразмера проволоки отдельно.
Контроль проволоки может осуществляться как в стационарном состоянии (на базе), так и в полевых условиях вблизи бурильных скважин.
В стационарном режиме контроль проводиться при перематывании проволоки с одной катушки на другую. Схема контроля показана на рис.1.
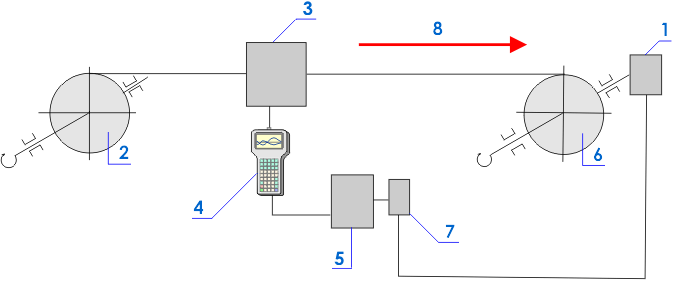
Приводной электродвигатель 1 вращает наматывающую катушку 6 с постоянной заданной частотой вращения. Проволока движется внутри направляющего устройства, совмещенного с измерительным датчиком 3. При вращении двигателя и, соответственно, перемотке проволоки с катушки 2 на катушку 6, измеряемое датчиками магнитное поле Hр (А/м) в виде графиков (магнитограмм) отображается на экране прибора 4. Катушка 2 вращается за счет перемотки проволоки на катушку 6. Контроль может проводиться одним или двумя операторами. В случае фиксирования на экране прибора резкого локального изменения магнитного поля Hр или его градиента (dHр/dx) выше предельного значения (указывается в методике) оператор пультом 7 останавливает приводной двигатель подачи проволоки и делает отметку краской или фломастером зоны концентрации напряжений.
Контроль по указанной на рис.1. схеме может осуществляться автоматически. При этом вся длина проволоки (до 15 км, длина может быть и больше при расширении объема памяти на приборах) может перематываться с катушки 2 на катушку 6 со скоростью 1,2-1,8 км/час, и одновременно с помощью датчика 3, имеющего автоматический счет длины, происходит запись диагностических параметров Hр и dHр/dx в долговременную память прибора типа ИКН-4М-16.
На рис.2. приведено фото специализированного сканирующего устройства Тип 13 для контроля проволоки.
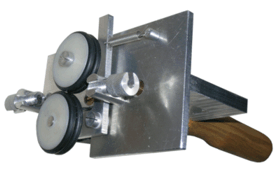
На рис.3. приведен фрагмент результатов контроля новой проволоки ⌀2,6 мм (ГОСТ 14959-79).
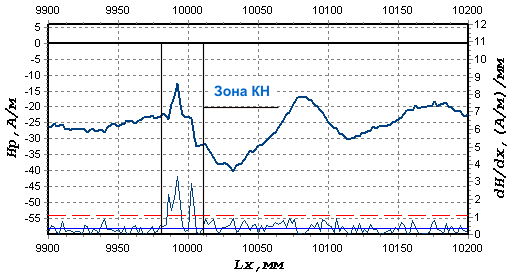
Контроль стальных канатов
Контроль стальных канатов выполняется с использованием специализированного сканирующего устройства Тип 15, охватывающего канат по всему периметру. Выявлена высокая эффективность метода МПМ при контроле, как отдельных витков, так и всего сечения каната.
На рис.4. представлены результаты контроля металла каната ⌀16 мм после наработки ~6700 циклов нагрузки на шахтном оборудовании.
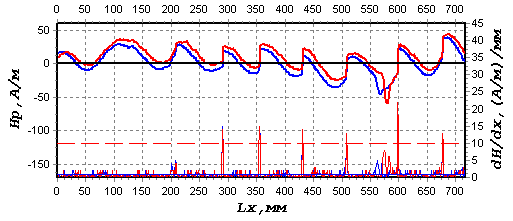