Определение механических свойств по параметрам твердости в зонах концентрации напряжений, выявленных в изделиях методом магнитной памяти металла
д.т.н. Матюнин В.М. (ФГБОУ ВО "НИУ "МЭИ")
д.т.н. Дубов А.А., к.т.н. Дубов Ал.А. (ООО "Энергодиагностика")
Известно, что основными источниками повреждений при эксплуатации изделий машиностроения являются локальные зоны концентрации напряжений (ЗКН), которые образуются под действием рабочих нагрузок в первую очередь на дефектах металлургического и технологического происхождения.
Проблемой контроля напряжений и деформаций в работающих конструкциях с целью оценки их состояния в настоящее время занимаются все ведущие диагностические центры мира. Однако известно, что эффективность методов контроля напряжений остается низкой при их использовании на практике. Особое значение приобретает повышение эффективности неразрушающего контроля (НК) напряженно-деформированного состояния (НДС) технических объектов при оценке их ресурса.
В настоящее время накопился большой арсенал методов и средств неразрушающего контроля остаточных напряжений (ОН) в изделиях машиностроения и напряженно-деформированного состояния (НДС) промышленных объектов в условиях эксплуатации. Однако при использовании их на практике возникает много организационных и научно-технических проблем, среди которых следует отметить:
- отсутствие метрологической базы для сертификации и поверки средств измерений характеристик НДС изделий (до сих пор в России и других странах нет единых эталонов, образцов и методик);
- непригодность большинства методов для контроля протяженных трубопроводов и крупногабаритных изделий, оборудования и сосудов;
- невозможность оценки НДС глубинных слоев металла изделий;
- отсутствие программ и центров обучения специалистов в области НК НДС;
- отсутствие стандартов, излагающих общие требования к методам и средствам НК напряжений и деформаций в реальных конструкциях.
Впервые такой стандарт подготовлен в России специалистами ООО "Энергодиагностика" совместно с ТК-132 Ростехрегулирования и опубликован в 2005 году как ГОСТ Р 52330-2005 "Контроль неразрушающий. Контроль напряженно-деформированного состояния объектов промышленности и транспорта. Общие требования".
Известно, что основными источниками повреждений оборудования и конструкций являются зоны концентрации напряжений (ЗКН), обусловленные технологическими дефектами изготовления, рабочими нагрузками или их сочетанием. Наличие ЗКН как на новых изделиях, так и на изделиях, бывших в эксплуатации, значительно снижает их ресурс. Поэтому контроль напряженно-деформированного состояния изделий и определение ЗКН с использованием средств неразрушающего контроля представляется в ГОСТ Р 52330-2005 наиболее важной задачей при контроле НДС. Именно для решения этой задачи - выявление ЗКН на основе 100% обследования оборудования и конструкций, предлагается использовать метод магнитной памяти металла (МПМ), который получает все большее распространение на практике.
После того, как выявлены ЗКН, при оценке ресурса требуется определить механические свойства металла в этих зонах. Однако, определение механических свойств металла в ЗКН, имеющих малую протяженность (от единиц до нескольких десятков мкм), весьма проблематично.
Из существующих методов контроля механических свойств для этих целей наиболее перспективен метод индентирования. Этот метод, известный под названием "безобразцовый метод", позволяет определять не только характеристики твердости, но и показатели других механических свойств металла, например, предел текучести (σ0,2), временное сопротивление (σв), равномерную деформацию (dр) и др. [1]. В основе безобразцового метода лежат корреляционные связи характеристик твердости с характеристиками прочности, но эти связи установлены для макроуровня, на котором деформируемые объемы металла при вдавливании индентора и растяжении образца сравнительно велики. При уменьшении деформируемых объемов металла начинает проявляться масштабный фактор, следствием которого является повышение определяемых значений твердости и прочности. Для ЗКН, имеющих малую протяженность, возможно применение только метода микротвердости, определяемой вдавливанием пирамиды. Однако значения микротвердости могут превосходить значения макротвердости в 1,5÷2 раза из-за влияния масштабного фактора.
Такое же увеличение твердости происходит и при вдавливании сферического индентора. Чем меньше диаметр индентора, тем выше твердость по Бринеллю, но при условии постоянства отношения диаметра отпечатка к диаметру индентора [2].
Аналогичное влияние оказывает масштабный фактор на характеристики прочности, определяемые растяжением образцов. Известно значительное увеличение прочности разрывных образцов диаметром менее 1 мм.
В связи с вышеизложенным, возникает вопрос о характере связи твердости и прочности на микро- и макроуровне и возможности их взаимного пересчета. Для обоснованного ответа на этот вопрос необходимо знать закономерности изменения характеристик твердости и прочности при переходе от макро- к микроуровню деформирования металла.
Для ответа на эти вопросы в лаборатории кафедры "Технология металлов" МЭИ были проведены специальные эксперименты на образцах одной марки стали при растяжении и вдавливании. В результате выполненных экспериментов были выявлены следующие два условия подобия. Первое условие обеспечивает одинаковые масштабные уровни при растяжении и вдавливании за счет равенства абсолютного изменения площади поперечного сечения образца ΔF и площади поверхности отпечатка М (ΔF=M). А второе условие обеспечивает при этом равенство относительных деформаций при растяжении образца ψрас и вдавливании индентора ψвд (ψрас=ψвд). Для выполнения этих условий целесообразно использование сферического индентора, который позволяет получать различные значения пластической деформации за счет изменения угла вдавливания в процессе одного нагружения.
Для количественной оценки средней пластической деформации при вдавливании сферического индентора ψвд предложена следующая формула [2]:
ψвд=1-[1-(d/D)2 ]1/2=0,5t/D=t/R, (1)
где d – диаметр отпечатка; t – глубина отпечатка; D – диаметр индентора; R – радиус скругления индентора.
Предложенные условия подобия и формула (1) позволяют подобрать необходимый исходный диаметр образца для растяжения dо по используемому диаметру индентора D.
В качестве материала для исследований был взят пруток диаметром 20 мм из стали 35. От прутка были отрезаны шайбы для испытаний на вдавливание и заготовки для изготовления разрывных образцов. Для проведения механических испытаний были изготовлены сферические инденторы с диаметрами D=0,1–10мм и цилиндрические пятикратные разрывные образцы с исходными диаметрами dо=0,6–10мм.
Испытания образцов на растяжение выполнялись на универсальной машине "Instron", позволяющей изменять шкалы нагрузок в зависимости от dо. При растяжении образцов различного диаметра были определены предел текучести σ0,2, временное сопротивление σв, абсолютные изменения площади поперечного сечения образцов на уровне предела текучести ΔF0,2 и на уровне временного сопротивления ΔFв.
Испытания вдавливанием инденторов различного диаметра выполнялись на модернизированном приборе МЭИ-Т7, снабженным встроенным микроскопом для измерения диаметров отпечатков и сменными силовыми пружинами для обеспечения требуемой точности измерения нагрузки. Конструкция прибора позволяет вдавливать индентор в одну и ту же точку с постепенным увеличением нагрузки и измерением диаметра отпечатка на каждой ступени нагружения. В результате таких испытаний можно получить диаграмму вдавливания. При вдавливании инденторов различного диаметра были определены твердость на уровне предела текучести НВ0,2 и соответствующая ей поверхность отпечатка М0,2, твердость на уровне временного сопротивления НВв и соответствующая ей поверхность отпечатка Мв. Методика определения НВ0,2 и НВв изложена в [3].
Результаты испытаний металла растяжением и вдавливанием показали, что при выполнении предложенных условий подобия отношения σ0,2/НВ0,2 и σв/НВв остаются одинаковыми на макро- и микроуровнях и примерно равны 1/3. Эти подобия обусловлены равенством энергий деформирования, возникающих при растяжении образца и при вдавливании индентора, так как сопротивление внешней нагрузке при обоих видах испытаний - это одновременно силомоментная и деформационная составляющие, которые в совокупности дают энергию сопротивления [4]. В этом проявляется физический смысл понятия "напряженно-деформированное состояние".
На рис.1 представлены экспериментальные зависимости σ0,2, σв от dо и НВ0,2, НВв от D, полученные по результатам испытаний растяжением и вдавливанием проволочных стальных образцов диаметром 150÷350мкм, предварительно отожженных для снятия наклепа.
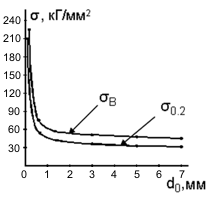
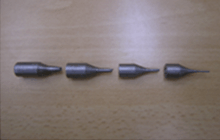
Рис.1a. Изменения σ0,2, σв в зависимости от dо
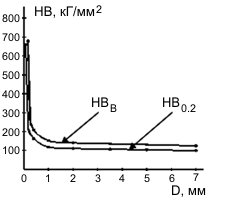
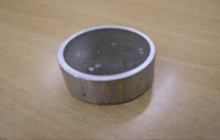
Рис.1б. Изменения НВ0,2 и НВв в зависимости от D
Для испытаний вдавливанием проволочных образцов изготовлялись специальные микрошлифы. Для этого отрезки проволок помещались в цилиндрическую металлическую обойму (рис.1, б), заполненную разогретым и размягченным полистиролом. Продольные оси отрезков выдерживались перпендикулярно основанию обоймы. После затвердевания полистирола торцы проволок, расположенные в одной плоскости, фрезеровались, шлифовались и полировались. В результате такой подготовки можно было вдавливать инденторы малого диаметра в торцы проволочных отрезков (рис.1). Для этого использовался индентор с радиусом скругления при вершине R=0,05мм (D=0,1мм). Из рис.1 видна явная аналогия в изменениях характеристик прочности и твердости, что свидетельствует об общих закономерностях влияния масштабного фактора при переходе от макро- к микроуровню деформирования металла. Причем, для проволочных образцов значения отношений σ0,2/НВ0,2 и σв/НВв также оказались примерно равным 1/3.
На участке зависимостей НВ0,2=f(D) и НВв=f(D) при D<1мм наблюдается значительное увеличение характеристик твердости. Аналогичное увеличение характеристик прочности наблюдается и на зависимостях σ0,2=f(dо) и σв=f(dо) при dо<1мм. Анализ экспериментальных данных показал, что эти участки можно аппроксимировать экспоненциальными зависимостями. Так, например, зависимости характеристик твердости НВ0,2 и НВв от D можно представить в следующем виде:
НВ0,2=Аexp(-aD); НВв=Вexp(-bD), (2)
где А, a, В, b - постоянные коэффициенты для данного материала.
Для определения коэффициентов, входящих в зависимости (2), достаточно определить два значения НВ0,2 (НВ0,2І и НВ0,2ІІ) и два значения НВв (НВвІ и НВвІІ) при вдавливании двух инденторов различного диаметра (DІ и DІІ):
a = [ln (НВ0,2І/ НВ0,2ІІ)] / (DІІ - DІ);
b = [ln (НВвІ/НВвІІ)] / (DІІ - DІ); (3)
А =НВ0,2І/ exp(-aDІ);
B =НВвІ/ exp(-bDІ). (4)
Эксперименты и расчеты показали, что для испытаний металла в ЗКН, имеющих протяженность не менее 200 мкм, можно использовать инденторы диаметром DІ=0,4мм и DІІ=1мм. При меньшей протяженности ЗКН необходимы инденторы меньшего диаметра.
Зная коэффициенты А, a, В, b, можно рассчитать значения характеристик твердости для такого диаметра индентора D, который будет соответствовать требуемому диаметру разрывного образца dо. В этом случае, используя зависимости, представленные на рис.1, возможен пересчет характеристик твердости НВ0,2 и НВв на характеристики прочности σ0,2 и σв.
Известно, что отношение σ0,2/σв является диагностическим параметром структурно-механического состояния металла ЗКН по методу МПМ. Если это отношение находится в пределах 0,5-0,8, то металл еще не склонен к хрупкому разрушению, и вероятность зарождения трещин низка. Однако, при увеличении этого отношения и приближении его к единице металл исчерпывает запас упрочняемости, его равномерная деформация очень мала, и вследствие этого контролируемая ЗКН представляет опасность, так как в ней могут образоваться трещины. В этом случае информацию о состоянии металла в ЗКН следует дополнить металлографическим анализом с помощью метода пластических реплик.
В таблице 1 приведены результаты диагностики механических свойств металла ЗКН в турбинной лопатке из стали 20Х13. Протяженность этой зоны составляла примерно 750мкм. Для определения механических свойств методом вдавливания использовались инденторы диаметром 0,4мм и 1мм. В таблице приведены не только диаметры инденторов D, но и диаметры образцов dо, которым соответствуют σ0,2 и σв при растяжении согласно предложенным условиям подобия.
Таблица 1
Результаты определения механических свойств металла в ЗКН и вне ЗКН турбинной лопатки
Механические свойства | Металл в ЗКН | Металл вне ЗКН | ||
---|---|---|---|---|
DІ = 0,4мм dо = 0,6мм |
DІІ = 1,0мм dо = 1,4мм |
D = 2,5мм dо = 3,5мм |
D = 2,5мм dо = 3,5мм |
|
НВ0,2, кГ/мм2 | 348 | 351 | 298 | 270 |
НВв, кГ/мм2 | 375 | 351 | 298 | 270 |
σ0,2, кГ/мм2 | 114,8 | 107,3 | 90,4 | 72,6 |
σв, кГ/мм2 | 123,8 | 115,8 | 98,3 | 89,1 |
σ0,2/ σв | 0,927 | 0,926 | 0,920 | 0,810 |
Как следует из таблицы 1, металл в ЗКН характеризуется высоким отношением σ0,2/ σв и поэтому является потенциально опасным из-за возможности образования трещин.
На рис.2 представлены результаты контроля шпильки (⌀60мм, сталь ЭП182) методом МПМ. Данная шпилька находилась в эксплуатации около 30 лет на фланцевом соединении цилиндра высокого давления турбогенератора ПТ-60-130. На рис.2, а показана схема контроля шпильки с ЗКН, выявленной методом МПМ. На рис.2, б показано распределение нормальной составляющей магнитного поля Hр и его градиента вдоль боковой поверхности шпильки, на которой были зафиксированы максимальные значения градиента поля dH/dx, характеризующие ЗКН.
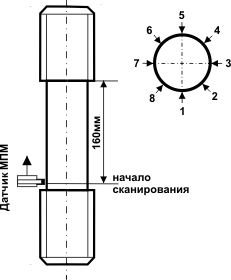
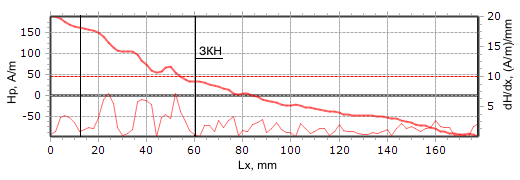
Затем в ЗКН данной шпильки были выполнены измерения твердости и определение механических свойств металла шпильки на приборном комплексе МЭИ-Т7 (рис.3).
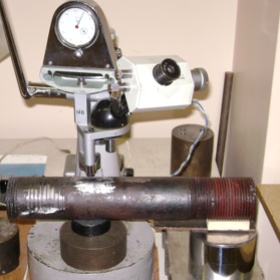
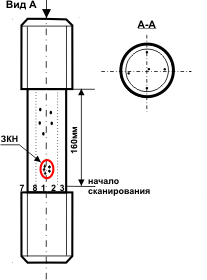
В таблице 2 представлены механические характеристики металла шпильки в ЗКН и вне этой зоны. Здесь следует отметить, что по опыту контроля шпилек методом МПМ, расположенных на фланцевых соединениях цилиндров турбогенераторов, случаи выявления ЗКН на боковых образующих шпилек нередки. Именно в этих ЗКН следует ожидать развития повреждений в процессе эксплуатации. Однако, согласно действующего в отрасли "Электроэнергетика" руководящего документа [5], контроль твердости шпилек рекомендуется осуществлять на торцах, считая, что шпильки по расчету работают на растяжение.
Таблица 2
Результаты определения механических свойств металла в ЗКН и вне ЗКН турбинной лопатки
Механические свойства | В ЗКН | Вне ЗКН |
С торца шпильки (средние величины) |
---|---|---|---|
D = 1,0мм | D = 1,0мм | ||
σ0,2, МПа | 810 | 570 | 604 |
σв, МПа | 980 | 750 | 788 |
δр, % | 5,6 | 7,4 | 7,1 |
НВ | 297 | 233 | 238 |
n | 2,06 | 2,08 | 2,07 |
δр, % - относительное равномерное удлинение;
n – характеристика деформационного упрочнения.
Из таблицы 2 видно, что механические свойства металла данной шпильки, полученные при измерениях с торца, находятся в удовлетворительном состоянии и соответствуют нормам (ГОСТ 20072-74). При этом механические свойства металла, измеренные в ЗКН, выявленной методом МПМ, имеют значения выше допустимого уровня.
Здесь следует также отметить, что значения σ0,2 и σв, полученные по результатам измерений твердости в ЗКН шпильки зависят от уровня остаточных напряжений (ОН) в этой зоне. Чем выше уровень ОН, тем больше значения твердости и других механических характеристик мы получим в результате указанных измерений. При этом оценку уровня ОН в ЗКН возможно выполнить методом МПМ, используя энергетическое соотношение между магнитными и механическими характеристиками, представленное в работе [6].
Литература
1. Марковец М.П. Определение механических свойств металлов по твердости. М.: Машиностроение, 1979. 191 с.
2. Матюнин В.М., Демидов А.Н., Проходцов М.А., Юзиков Б.А. Влияние масштабного фактора на результаты определения твердости методом Бринелля // Технология металлов, 2008, №8. С.49-52.
3. Матюнин В.М. Оперативная диагностика механических свойств конструкционных материалов. М.: Издательский дом МЭИ, 2006. 214 с.
4. Марковец М.П. Власов В.Т., Дубов А.А. Физическая теория процесса «деформация-разрушение». Ч. I. Физические критерии предельных состояний металла. М.: ЗАО "Тиссо", 2007. 517 с.
5. РД 10-577-03. Типовая инструкция по контролю металла и продлению срока службы основных элементов котлов, турбин и трубопроводов тепловых электростанций. М.: ОАО "НТЦ "Промышленная безопасность", 2007.
6. Дубов А.А., Дубов Ал.А., Колокольников С.М. Метод магнитной памяти металла и приборы контроля. Учебное пособие. М.: ЗАО "Тиссо", 2008. 363 с.