Назначение и практические возможности метода магнитной памяти металла
д.т.н., профессор Дубов А.А.
Принципиальные отличия метода магнитной памяти металла (МПМ) от других магнитных методов неразрушающего контроля (НК) отмечались неоднократно в статьях [1, 2, 3] и в теоретических работах [4, 5, 6].
Основное назначение метода МПМ – определение на оборудовании и в конструкциях в режиме экспресс-контроля с использованием специализированных приборов и сканирующих устройств зон концентрации напряжений (ЗКН) – основных источников развивающихся повреждений.
ЗКН – это не только заранее известные области, где особенности конструкции создают различные условия для распределения напряжений, создаваемых внешней нагрузкой, но и случайно расположенные области, где в силу начальной неоднородности металла в сочетании с нерасчетными дополнительными рабочими нагрузками возникают большие деформации (как правило, деформации сдвига).
Геометрическим признаком магнитных аномалий, характеризующим ЗКН, является расстояние между экстремальными значениями собственного магнитного поля, кратное типоразмеру изделия (толщине, ширине, диаметру). Это расстояние соответствует минимальному расстоянию между соседними площадками скольжения или критическому размеру оболочки, возникающему, например, при потере устойчивости трубы.
Контроль методом МПМ осуществляется без зачистки металла и искусственного намагничивания. Используется остаточная намагниченность, которая сложилась естественным образом при изготовлении изделий и в процессе их эксплуатации.
Можно, конечно, сомневаться в том, что возможно выявление ЗКН и различных дефектов металла по магнитным аномалиям с неизвестной предысторией изделий [7]. Однако, известно, что критерий истины - практика! Многочисленные исследования, выполненные авторами метода на заводах-изготовителях, показали, что все однотипные изделия, изготовленные из одной марки стали и по одной технологии, имеют практически одинаковое распределение остаточной намагниченности, и только в зонах концентрации остаточных напряжений и различных неоднородностей структуры на отдельных изделиях при контроле фиксируются магнитные аномалии. И это не удивительно, так как при формировании, например, термоостаточной намагниченности изделий в процессе их изготовления определяющую роль играют внутренние напряжения, а не слабое внешнее геомагнитное поле.
При эксплуатации изделий исходная остаточная намагниченность (ОН) перераспределяется под действием рабочих нагрузок, и в ЗКН возникают магнитные аномалии, обусловленные геометрическими смещениями и типоразмером изделия.
Если в однотипных изделиях под действием рабочих нагрузок не возникают локальные ЗКН, то характер распределения ОН в них практически одинаковый. Для того чтобы убедиться в этом, необходимо было обследовать несколько тысяч однотипных узлов и изделий! На основе установленных закономерностей и значительного практического опыта обследования различных узлов оборудовании и конструкций авторами предложена методология безэталонной калибровки средств и методов контроля и соответствующая их метрология [3].
Диагностические параметры в методе МПМ:
1. Согласно ГОСТ Р ИСО 24497-1-2009 [8] метод МПМ - метод неразрушающего контроля, основанный на регистрации и анализе распределения собственных магнитных полей рассеяния (СМПР), возникающих на изделиях и оборудовании в зонах концентрации напряжений (ЗКН).
СМПР, отображающее остаточную намагниченность, сформировавшуюся естественным образом в процессе изготовления изделия, следует отличать от магнитных полей рассеяния (МПР), возникающих на дефектах металла и трещинах при искусственном намагничивании изделия (например, при выполнении магнитопорошковой дефектоскопии).
2. Для количественной оценки уровня концентрации напряжений (источников повреждений) определяется градиент нормальной (Hy) и/или тангенциальной (Hx) составляющих СМПР:
Kин = |ΔHy| / Δx, при Δx->0 Kин = dH / dx, (1)
где Δx - расстояние между соседними точками контроля.
В отдельных случаях при контроле напряженно-деформированного состояния (НДС) оборудования используется градиент результирующего СМПР:

3. Среди основных расчетных диагностических параметров в методе МПМ применяется параметр m, характеризующий предельную деформационную способность материала:
m = Кинmax / Кинcp, (2)
где Кинmax и Кинcp, соответственно, максимальное и среднее значения градиента поля, которые определяются при контроле методом МПМ однотипных узлов оборудования.
В ходе промышленных и лабораторных исследований на образцах установлено соотношение между предельными значениями магнитных и механических параметров:
mпр = Кинmax / Кинср ≈ Кинпр / Кинв ≈ σпр / σв, (3)
где значения Кинmax и Кинср, полученные в результате контроля однотипных узлов оборудования, соответствуют значениям Кинпр и Кинв, полученным в результате испытаний на растяжение образцов, изготовленных из той же марки стали, при достижении, соответственно, истинного предела прочности при разрушении σпр и условного предела прочности σв.
В экспериментальных исследованиях было установлено также, что, если фактический параметр mф ≥ mпр, то в этом случае в металле контролируемого узла оборудования возникает предельное (критическое) состояние, при котором образуется макротрещина. Физическое обоснование параметра mпр приведено в работах [3, 4, 5].
Здесь следует отметить, что раскрытие микротрещин при достижении предельного состояния металла составляет доли миллиметров, что является зоной нечувствительности для большинства методов НК. Поэтому некорректно сравнивать результаты контроля по методу МПМ, например, с результатами по УК, рентгену или ВК. И какие-либо замечания в адрес метода МПМ по перебраковке или недобраковке не приемлемы. Подтверждающими для результатов контроля в ЗКН с предельным состоянием металла являются металлография, измерение твердости или контроль, например, ультразвуком на поисковом уровне.
При значениях фактического магнитного параметра mф значительно больше mпр, т.е. mф > mпр, размеры трещин или различных дефектов в ЗКН становятся соизмеримыми с браковочными по существующим нормам для УК, рентгена и др. И в этом случае, при дополнительном контроле другими методами НК, такие дефекты выявляются.
Однако проблема состоит в определении этих областей непосредственно на металле оборудования и сварных соединениях из-за малых размеров ЗКН и отсутствия сведений о месте их расположения. Места возникновения ЗКН, как правило, не совпадают с расчетными данными. В сочетании результатов контроля по методу МПМ с другими методами НК резко повышается эффективность контроля. Именно при таком комплексном контроле основного металла и сварных соединений в настоящее время широко используется метод МПМ. В режиме экспресс-контроля без какой-либо подготовки поверхности методом МПМ выявляются ЗКН на объекте контроля (ОК), выполняется их классификация по градиенту СПМР и по расчетному параметру m, и затем в назначенных ЗКН делается дополнительный контроль ультразвуком или другими методами НК.
Рассмотрим далее отдельные примеры из практики применения метода МПМ.
На рис.1 показана схема контроля сварных швов трубопроводов и сосудов с применением сканирующего устройства Тип 1-8М и прибора типа ИКН (измерителя концентрации напряжений).
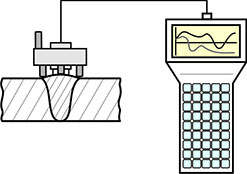
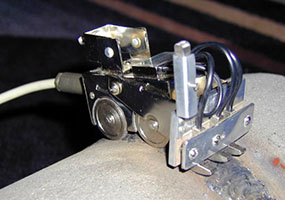
Рис.1. Схема контроля сварных швов сосудов с применением сканирующего устройства Тип 1-8М и прибора типа ИКН.
На рис.2 приведены результаты контроля методом МПМ кольцевого сварного шва реактора полимеризации на предприятии "Anwil" (Влоцлавек, Польша).
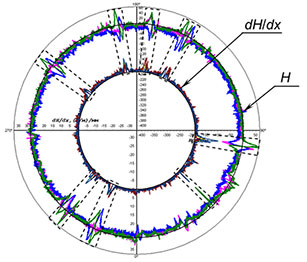
Наружная часть круговой магнитограммы соответствует СМПР (H), а внутренняя часть – распределению градиента СМПР (dH/dx) вдоль периметра сварного шва. Пунктирными линиями выделены ЗКН, выявленные при контроле. Во всех ЗКН было рекомендовано выполнить дополнительный ультразвуковой контроль (УК).
После сопоставления результатов контроля методами МПМ и УК установлен браковочный уровень допустимых дефектов по градиенту СМПР (dH/dx). В дальнейшем, этот браковочный уровень использовался при контроле методом МПМ аналогичных сварных швов.
На рис.3 представлен фрагмент контроля газопровода через слой изоляции с использованием сканирующего устройства (СУ) с высокочувствительными датчиками измерения СМПР.
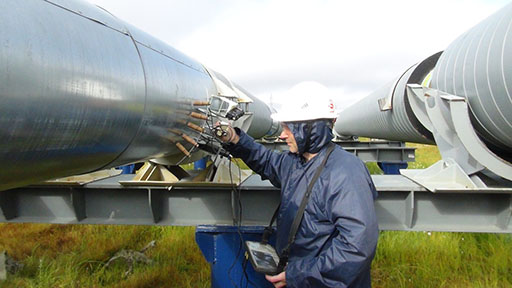
Трубопроводы в пенополиуретановой (ППУ) изоляции стали широко применяться с целью снижения коррозионного износа металла. Однако, на трубопроводах в ППУ-изоляции, из-за меньшей потери тепла от металла трубы по сравнению с обычной изоляцией, перемещение трубы при самокомпенсации больше и, соответственно, уровень напряжений в зонах их концентрации больше. Кроме того, при расположении трубопроводов на опорах, установленных в зонах с нестабильными грунтами и в заболоченных местах, возникает проблема обеспечения расчетных перемещений, способствующая образованию повреждений. При этом основным местом образования ЗКН являются зоны термического влияния (ЗТВ) монтажной сварки. Некачественная монтажная сварка в сочетании с высоким уровнем напряжений при недостатке самокомпенсации температурных расширений являются причиной образования трещин в ЗТВ сварки.
На рис.4 показаны результаты контроля методом МПМ участка нефтепровода ⌀ 820 × 10 мм, расположенного на опорах вблизи П-образного компенсатора. В верхней части магнитограммы показано распределение СМПР (H), а в нижней части – градиента dH/dx, измеренные вдоль поверхности изоляции. Из рис.4 видно, что вблизи опоры № 1, в сравнении с опорой № 2, зафиксирована аномалия в распределении СМПР, которая характеризует образование ЗКН.
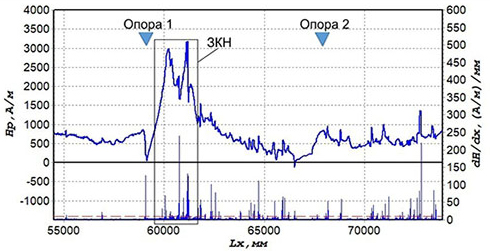
После снятия изоляционной муфты на сварном монтажном стыке, расположенном в ЗКН, был сделан контроль методом МПМ непосредственно по металлу трубы вдоль периметра этого стыка непосредственно по металлу трубы. На рис.5, а представлена магнитограмма, зафиксированная при контроле стыка методом МПМ. В нижней части данного стыка выявлено несколько локальных ЗКН, характеризующихся высокими значениями градиента СМПР (dH/dx). Затем в этих зонах был выполнен ультразвуковой контроль. По результатам УК на этом стыке были выявлены недопустимые дефекты в виде протяженных несплошностей в ЗТВ на глубине от 8 до 10 мм (вблизи корня шва). На рис.5, б для сравнения показана магнитограмма, зафиксированная на монтажном сварном стыке, расположенном вблизи опоры № 2 без ЗКН. Видно, что градиент СМПР (dH/dx) на этом стыке имеет относительно равномерное распределение. При выполнении УК на этом стыке недопустимых дефектов не обнаружено.
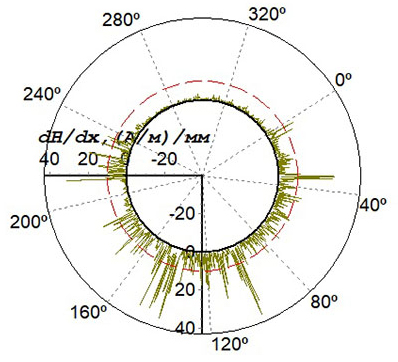
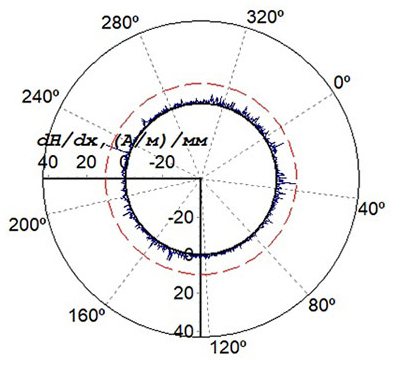
Рис.5. Результаты контроля методом МПМ монтажного кольцевого стыка, расположенного в ЗКН (а), и монтажного кольцевого стыка, имеющего по результатам МПМ удовлетворительное состояние (б).
На нефтепроводе ⌀ 820 × 10 мм были вскрыты еще 9 сварных монтажных стыков, расположенных в ЗКН вблизи опор, и на всех стыках при дополнительном НК методами МПМ и УК непосредственно по металлу выявлены недопустимые дефекты в виде несплошностей в ЗТВ.
Одной из проблемных задач в обеспечении надежности вращающихся механизмов является предотвращение внезапных усталостных повреждений валов, роторов дисков, лопаток и других узлов турбинных и компрессорных установок. Именно для решения этой задачи эффективно использовать магнитомеханическую память металла, обусловленную гистерезисом. Остаточная намагниченность, сложившаяся под действием фактических рабочих нагрузок, и измеряемое СМПР контролируемых узлов напрямую отображают формирование ЗКН – источников повреждений на самом раннем этапе их развития.
На рис.6 представлены магнитограммы, зафиксированные при контроле в 2019 году лопаток № 15 и № 17 ступени № 9 ротора паровой турбины К-15-41 цеха производства аммиака АО "ОХК "Уралхим" (Кирово-Чепецк).
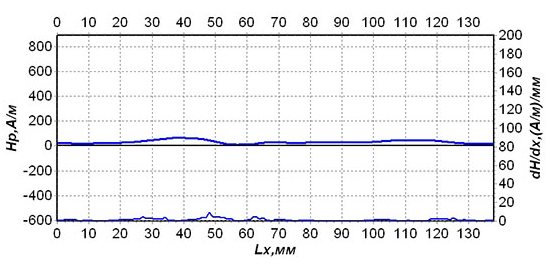
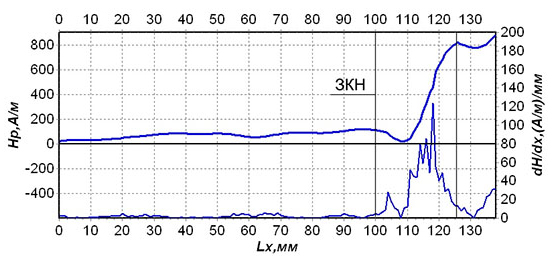
Рис.6. Результаты контроля методом МПМ лопаток № 15 (а) и № 17 (б) ступени 9 турбины К-15-41.
Лопатки ступени № 9 на дату контроля имели наработку ~190000 час. Однако из рис.6 видно, что эти лопатки по результатам контроля методом МПМ имеют различное состояние. На лопатке № 17 (рис.6, б) установлено резкое локальное изменение магнитного поля H и его градиента (dH/dx), характеризующее ЗКН. При дополнительном контроле механических свойств путем измерения твердости в ЗКН лопатки № 17 отмечено снижение твердости по Бриннелю (HB) до величины 188-192 кгс/мм2. Значение твердости (HB) на лопатке № 15 оказалось в пределах 216-225 кгс/мм2, допустимых для стали 20Х13. На отдельных лопатках этой ступени в ЗКН зафиксировано упрочнение: величина твердости (НВ) достигала 260 кгс/мм2.
В процессе длительного циклического нагружения лопаток поверхностный слой вначале упрочняется, а затем разупрочняется ("разрыхляется") из-за образования микротрещин. Поэтому, для обеспечения надежности лопаток с выявленными ЗКН в условиях отсутствия возможности их замены рекомендуется выполнять шлифовку поверхности с удалением поврежденного слоя металла.
В заключение необходимо еще раз отметить основное назначение метода МПМ и области его применения:
- экспресс-контроль качества изделий машиностроения с целью выявления дефектов металла и локальных ЗКН;
- ранняя диагностика коррозионно-усталостных повреждений и оценка остаточного ресурса оборудования и конструкций;
- определение дефектов (расслоения, дефектов литья и других) в глубинных слоях металла за счет использования геометрических параметров СМПР, обусловленных площадками скольжения дислокаций в ЗКН;
- 100% обследование ОК с целью выявления локальных ЗКН – источников развития повреждений;
- повышение эффективности неразрушающего контроля ОК за счёт применения метода МПМ в комплексе с другими методами НК;
- сокращение материальных затрат на выполнение контроля за счёт отказа от искусственного намагничивания ОК и зачистки поверхности (а в отдельных случаях – от снятия изоляции с ОК).
С использованием метода МПМ предоставляется возможность исследовать структурные и механические свойства металла на физическом уровне при испытании образцов в лабораторных условиях.
Область применения метода МПМ распространяется на любые изделия, изготовленные из ферро- и парамагнитного материала. В настоящее время в энергетике, нефтехимии, нефтяной, газовой и других отраслях промышленности России метод МПМ включен в ряд руководящих документов и отраслевых стандартов (более 60 документов).
Литература
1. Дубов А.А. Принципиальные отличительные признаки метода магнитной памяти металла и приборов контроля в сравнении с известными магнитными методами неразрушающего контроля // Контроль. Диагностика. 2003. № 12. С. 27-29.
2. Дубов А.А. Принципиальные отличия метода магнитной памяти металла от других известных магнитных методов неразрушающего контроля. Итоги и перспективы развития метода // Территория NDT. 2016. № 2. C. 64-68.
3. Дубов А.А. Метрологические аспекты в методе магнитной памяти металла // Мир измерений, 2018, № 3. С.42-45. №4. С.16-184.
4. Власов В.Т., Дубов А.А. Физические основы метода магнитной памяти металла. М.: ЗАО "Тиссо", 2004. 424 с.
5. Власов В.Т., Дубов А.А. Физическая теория процесса "деформация-разрушение". Ч.I. Физические критерии предельных состояний металла. М.: ЗАО "Тиссо", 2007. 517 с.
6. Власов В.Т., Дубов А.А. Физическая теория процесса "деформация-разрушение". Ч. II. Термодинамика процесса. М.: ИД "Спектр", 2016. 228 с.
7. Горкунов Э.С., Ефимов А.Г., Шубочкин А.Е., Артемьев Б.В. К вопросу применения магнитного НК для определения напряженно-деформированного состояния металлоконструкций // В мире НК, 2016, № 3. С. 52-55.
8. ГОСТ Р ИСО 24497-1-2009. Контроль неразрушающий. Метод магнитной памяти металла. Часть 1. Термины и определения.
9. ГОСТ Р ИСО 24497-2-2009. Контроль неразрушающий. Метод магнитной памяти металла. Часть 2. Общие положения.
10. ГОСТ Р ИСО 24497-3-2009. Контроль неразрушающий. Метод магнитной памяти металла. Часть 3. Контроль сварных соединений.
11. Дубов А.А. Мониторинг рисков на основе ранней диагностики состояния металла оборудования и конструкций в зонах концентрации напряжений - источников развития повреждений // Химическая техника. 2016. № 4. С. 26-28.
12. Дубов А.А. Новые требования к методам и средствам диагностики напряженно-деформированного состояния материалов // Мир измерений. 2012. № 6. С. 38-42.
13. ГОСТ Р 52330-2005. Контроль неразрушающий. Контроль напряженно-деформированного состояния объектов промышленности и транспорта. Общие требования.
14. ГОСТ Р 53006-2008. Оценка ресурса потенциально опасных объектов на основе экспресс-методов. Общие требования.