Метод магнитной памяти металла и его возможности для диагностики элементов энергетических котлов
д.т.н., профессор Дубов А.А.
В статье рассматриваются причины повреждений котельных труб и существующие проблемы в диагностике этих повреждений на раннем этапе их развития. Представлены возможности метода магнитной памяти металла для ранней диагностики развивающихся повреждений гибов паропроводных и экранных труб энергетических котлов.
Основными источниками разрушения труб поверхностей нагрева (ПН) являются зоны концентрации механических напряжений (ЗКН), в которых процессы коррозии, ползучести и усталости протекают наиболее интенсивно. Концентрация напряжений на отдельных участках обусловлена, в основном, недостатком самокомпенсации труб и возникает из-за различных нарушений и отступлений от проектной схемы перемещений труб в подвижных креплениях, допускаемых при монтаже и ремонте котлов; повышения теплогидравлической разверки; неправильной установки ремонтных вставок; защемления труб в ремонтных "сухарях" и в местах прохода труб и змеевиков через обмуровку. Своевременное выявление участков труб с максимальной концентрацией напряжений является главной задачей, решаемой методом диагностики, основанном на эффекте магнитной памяти металла (МПМ).
На метод МПМ имеются международные стандарты ISO 24497-1:2007(Е), 24497-2:2007(Е), 24497-3:2007(Е). На основе международных стандартов введены в действие национальные стандарты в России, Украине, Польше, Китае, Монголии, Иране. В России метод МПМ Ростехнадзором включен в перечень основных методов неразрушающего контроля, рекомендуемых для применения на опасных промышленных объектах (ОПО). Действуют более 50 руководящих документов Ростехнадзора для различных отраслей промышленности, в которых метод МПМ рекомендован для контроля трубопроводов, сосудов, оборудования и конструкций. В 2011 году получен сертификат TUV Rheinland Inter Cert Kft (01202 HU/V 11-3420), допускающий применение метода МПМ на ОПО.
Известно, что трубы в состоянии поставки имеют определенный уровень остаточной намагниченности, сложившейся в процессе их изготовления. В условиях монтажа остаточная намагниченность изменяется и перераспределяется под действием сварочных и монтажных напряжений. При эксплуатации котельных труб остаточная намагниченность, сформировавшаяся в процессе изготовления и монтажа, изменяется под действием рабочих нагрузок.
В специальных лабораторных и промышленных экспериментах установлено, что перераспределение остаточной намагниченности и, соответственно, собственного магнитного поля рассеяния (СМПР) Hр на поверхности труб обусловлено действием магнитоупругого, магнитомеханического эффектов и магнитопластики [1]. Установлено также, что изменение остаточной намагниченности и, соответственно, измеряемого поля Hр при растяжении, сжатии, кручении и циклическом нагружении ферромагнитных труб однозначно связано с максимально действовавшими рабочими напряжениями, что позволило использовать этот параметр как элемент памяти при разработке данного метода диагностики.
Известно, что потеря устойчивости труб происходит при достижении осевой силой значения критической нагрузки. При этом происходит, как правило, упругопластический прогиб трубы, исчезающий (или частично исчезающий) после снятия осевой нагрузки.
В условиях работы котельной трубы на участке, имеющем недостаток самокомпенсации (например, при наличии защемления в узлах креплений) при потере устойчивости, как правило, возникает изгиб с кручением. В ослабленном сечении такого участка трубы образуется соответствующее поле напряжений и плоскости сдвига с максимальной деформацией металла. В этой же зоне на поверхности трубы возникают устойчивые полосы и площадки скольжения дислокаций задолго до достижения условного предела текучести металла. Устойчивые полосы скольжения возникают и в случаях локального перегрева металла вследствие недостатка самокомпенсации по периметру и толщине стенки трубы. Момент возникновения устойчивых площадок скольжения дислокаций связан с уровнем и направлением внутренних напряжений (напряжений растяжения, сжатия, сдвига). Устойчивые полосы скольжения дислокаций, возникающие под действием повторяющихся в одном и том же месте циклических нагрузок, могут получить развитие до каналов с размерами по глубине и ширине до десятков и сотен микрон, что уже будет заметно на макроуровне. По границам этих каналов происходит развитие пластической деформации и, в итоге, зарождение трещин.
Многолетний опыт исследования магнитных полей на котельных и паропроводных трубах выявил наличие устойчивых линий смены знака нормальной составляющей напряженности магнитного поля Hр в зонах развивающихся повреждений металла (линий Hр=0). Интерпретация этого диагностического магнитного параметра как линии максимальных напряжений, возникающей на поверхности труб под действием рабочих нагрузок, подтверждена расчетными исследованиями [2, 3]. Очевидно, что совпадение линий Hр=0 со сварными стыками и гибами наиболее опасно для надежности труб ПН.
Для количественной оценки уровня концентрации напряжений определяется градиент (интенсивность изменения) нормальной и/или тангенциальной составляющих магнитного поля Hр [4]:
Кин=|ΔHр|/Δx (1)
где Кин - градиент магнитного поля рассеяния, характеризующийся интенсивностью изменения намагниченности металла в зоне концентрации напряжений (ЗКН) и, соответственно, интенсивностью изменения поля Hр; |ΔHр|– модуль разности поля Hр между двумя точками контроля; Δx – расстояние между двумя точками контроля.
Предложенные в методике критерии позволяют отличать участки труб, работающие в упругой зоне деформаций металла от участков, работающих в зоне пластической деформации металла и находящихся в состоянии предразрушения металла.
Как правило, нулевые линии нормальной составляющей магнитного поля (линии Hр=0) соответствуют зонам концентрации напряжений, являющимися источниками развития повреждений труб. Однако, в отдельных случаях развитых локальных дефектов (например, язвины коррозии) имеет место локальное изменение поля Hр без изменения знака. Общим признаком ЗКН и развитых дефектов является резкое локальное изменение поля Hр и его градиента Кин. Зоны с максимальной концентрацией напряжений соответствуют зонам с максимальными градиентами поля Кин.
Рассматриваемый магнитный метод диагностики поверхностей нагрева (ПН) может быть использован самостоятельно и в сочетании с другими разрушающими и неразрушающими методами контроля.
Для выполнения контроля котельных труб используются приборы типа ИКН (измерители концентрации напряжений магнитометрические) и специализированные сканирующие устройства (СУ), изготавливаемые ООО "Энергодиагностика".
Контроль выполняется на остановленном в ремонт или резерв котле. Для проведения измерений напряженности магнитного поля рассеяния (Hр) вдоль образующих труб контролируемой поверхности нагрева специальной зачистки не требуется, но шлаковую корку необходимо удалить.
Выполнение контроля осуществляют два оператора. Один из них выполняет сканирование датчиком прибора вдоль поверхности трубы. Другой оператор производит запись измеренных величин Hр в журнал регистрации результатов контроля.
Допускается проводить контроль только одному оператору, при условии соблюдения правил техники безопасности, а также при наличии у оператора соответствующей квалификации и опыта контроля.
Рассмотрим далее отдельные примеры из практики применения метода МПМ при диагностике котельных и паропроводных труб.
В настоящее время на тепловых и атомных электростанциях существует проблема обнаружения ЗКН на гибах паропроводных труб, являющихся источниками развития повреждений.
На рис.1 представлены результаты контроля методом МПМ растянутой зоны гиба ⌀219x19 мм, ст.15Х1МФ. На рис.1, а показана схема контроля гиба, а на рис.1, б - сканирующее устройство, используемое при контроле. На рис.1, в представлена магнитограмма, зафиксированная при контроле. На верхней части магнитограммы показано распределение собственного магнитного поля гиба, а в нижней части - распределение градиента этого поля.
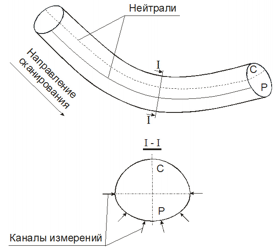
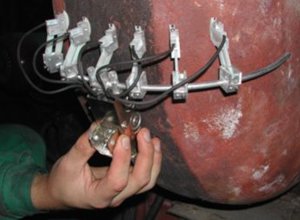
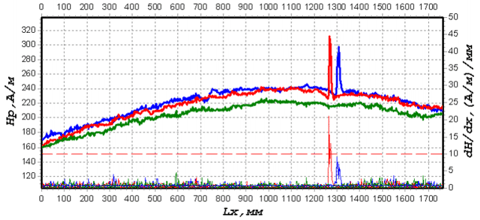
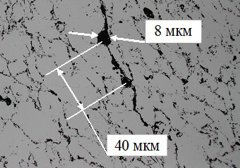
Рис.1. Результаты контроля методом МПМ растянутой зоны гиба ⌀219x25 мм (ст.15Х1МФ) пароперепускной трубы: а - схема контроля гиба; б - сканирующее устройство, используемое при контроле; в - распределение магнитного поля Hр и его градиента dHр/dх вдоль растянутой образующей гиба; г - структура металла, зафиксированная в зоне локального изменения магнитного поля.
В зоне резкого локального изменения поля и его градиента с поверхности гиба была взята "реплика" для анализа структуры металла. На рис.1,г представлена структура металла, зафиксированная в зоне локального изменения магнитного поля. В данном случае для удаления поврежденного слоя металла с наружной поверхности была выполнена шлифовка металла на глубину 100-150 мкм. После удаления поврежден-ного слоя металла в ЗКН гиб был допущен в дальнейшую эксплуатацию.
Рассмотрим другой пример применения метода МПМ. В настоящее время существует проблема определения язвин коррозии на внутренних поверхностях нагрева энергетических котлов.
На рис.2, а показаны результаты контроля экранной трубы ⌀60x6мм (ст.12Х1МФ) мощного энергетического котла. На рис.2, б показан вырезанный участок трубы из ЗКН, выявленной методом МПМ. На внутренней поверхности вырезанного участка трубы были обнаружены язвины коррозии.
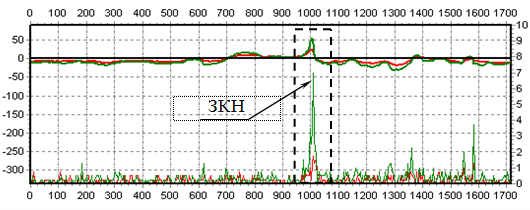
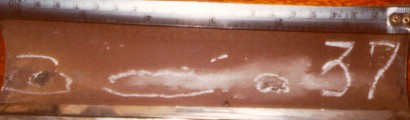
Рис.2. Результаты контроля экранной трубы ⌀60x6мм фронтового экрана котла ТГМП-206.
Известно, что газоплотные панели обеспечивают уплотнение топки от присосов холодного воздуха, увеличивают площадь поверхностей нагрева и, таким образом, повышают экономичность котлов. Однако, с самого начала эксплуатации котлов с газоплотными панелями была выявлена их низкая ремонтопригодность. Кроме того, в процессе эксплуатации была обнаружена более высокая чувствительность газоплотных панелей к теплогидравлическим разверкам и, особенно, к локальным перегревам металла. Даже незначительные нарушения соотношений "вода-топливо" или "топливо-воздух", допускаемые для обычных котлов, могут вызвать массовые повреждения труб газоплотных панелей с выходом их из строя.
На рис.3 представлен фрагмент повреждений труб газоплотных панелей заднего экрана в виде массового их прогиба в зоне монтажных сварных стыков. Такой вид повреждений был выявлен специалистами ООО "Энергодиагностика" в марте 2004 года на газоплотном котле 525т/час, ст.№4 ТЭС "Дора" (Ирак).
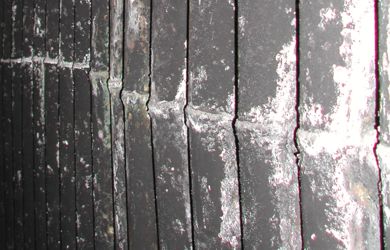
Аналогичные повреждения имеют место на газоплотных котлах электростанций России.
Очевидно, что эксплуатация и ремонт котлов с газоплотными панелями требуют более высокого уровня квалификации персонала электростанций, обслуживающего эти котлы. Очевидно также, что технология ремонта газоплотных панелей требует совершенствования и применения современных методов технической диагностики.
При исследовании напряженно-деформированного состояния (НДС) труб газоплотных панелей с использованием метода МПМ установлено, что более 90% всех ЗКН и развивающихся в них повреждений расположено вблизи заводских, монтажных и ремонтных сварных стыков. Только в отдельных случаях ЗКН и повреждения в них происходят на участках труб, расположенных меду сварными стыками. Установлено также, что повреждения металла находятся преимущественно в зонах термического влияния (ЗТВ) сварки, являющимися, как известно, технологическими и конструктивными концентраторами напряжений. Установленная закономерность преимущественного расположения повреждений труб вблизи сварных стыков характерна для газоплотных котлов и очевидно обусловлена их конструктивными особенностями и принципиально другим распределением напряжений и деформацией при температурной компенсации по сравнению с экранными трубами, имеющими подвижные узлы креплений через каждые 2-4м по высоте топки. В случае недостатка самокомпенсации отдельной трубы и/или нескольких труб внутри газоплотной панели распределение возникающих при этом напряжений и деформаций на каждой трубе в отдельности обусловлено взаимным влиянием всей массы труб, жестко связанных между собой внутри панели. При этом наиболее восприимчивыми к напряжениям от недостатка температурной компенсации оказываются ЗТВ сварки, как наиболее слабое звено по условиям прочности.
В подтверждение сказанного рассмотрим пример из практики применения метода МПМ при диагностике НДС газоплотных панелей.
На рис.4 представлены результаты контроля отдельных труб газоплотных панелей на котле 525 т/час, ст.№ 4 ТЭС "Дора" (Ирак). Видно, что вблизи монтажных сварных стыков зафиксировано резкое увеличение магнитного поля Hр и его градиента dHр/dх.
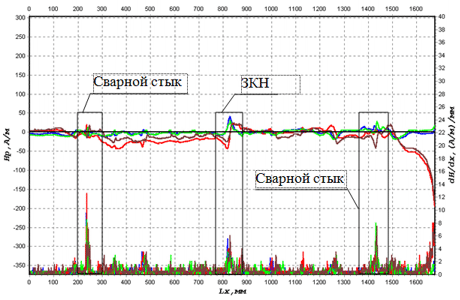
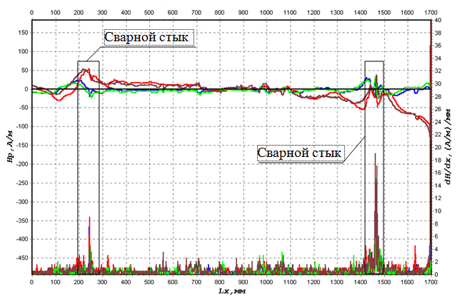
Рис.4. Результаты контроля трубы №26 (а) и трубы №28 (б) фронтового экрана на уровне верхнего яруса горелок котла №4 ТЭС "Дора" (Ирак).
Представленные на рис.4 фрагменты распределения магнитного поля являются характерными для отдельных труб внутри панелей. Путем вырезки образцов и анализа их состояния установлено, что именно на участках труб с максимальным значением градиента магнитного поля развиваются повреждения металла. Характер повреждений в ЗКН, расположенных вблизи сварных стыков, может быть разным в зависимости от ряда эксплуатационных факторов. На основе выполненных исследований состояния металла образцов, вырезанных из участков труб с ЗКН, установлено, что повреждения могут развиваться как с внутренней поверхности, так и с наружной.
Повреждение в ЗКН преимущественно развивается на внутренней поверхности трубы в случае низкого качества котловой воды и с наружной поверхности при наличии агрессивных компонентов в топочных газах (например, при сжигании низкокачественного топлива и недостатке воздуха). На внутренней поверхности труб повреждения развиваются, как правило, в виде отдельных язвин или цепочки язвин (рис.2), а на наружной поверхности - в виде поперечных рисок с частотой, кратной толщине стенки трубы.
В работах [5, 6] рассматриваются возможности метода МПМ при решении различных задач обеспечения надежности труб поверхностей нагрева энергетических котлов. В частности, в указанных работах [5, 6] рассматриваются возможности метода МПМ при выявлении участков с развивающимися повреждениями из-за перегрева металла, при контроле сварных соединений в узлах с контактной сваркой и в узлах приварки змеевиков к коллекторам, при определении межкристаллитной коррозии на аустенитных трубах, при выявлении мест защемлений на трубах и в опорно-подвесной системе котлов, вызывающих развитие повреждений из-за недостатка самокомпенсации температурных расширений.
В заключение следует отметить, что до сих пор на большинстве тепловых электростанций и в котельных России основным мероприятием по обеспечению надежности котельных труб в случае возникновения их повреждений является массовая замена труб. Одной из причин такого подхода к обеспечению надежности котлов является отсутствие эффективных методов для ранней диагностики участков труб с развивающимися повреждениями. На основе длительного периода (более 30 лет) применения метода МПМ на ряде энергетических и водогрейных котлов электростанций России, Польши, Китая, Болгарии, Индии и других стран можно заявить об эффективности метода при решении указанных задач.
Литература
1. Власов В.Т., Дубов А.А. Физические основы метода магнитной памяти металла. М.: ЗАО "Тиссо", 2004. 424 с.
2. Встовский Г.В., Дубов А.А. Решение обратной задачи расчета полей напряжений в стенках труб по магнитным полям рассеяния на основе нелинейной модели магнитоупругого эффекта // Заводская лаборатория, 2000, №3.
3. Кулеев В.Г., Дубов А.А., Лопатин В.В. Нулевые линии нормального поля рассеяния на поверхности бездефектной трубы при ее упругом изгибе в любом внешнем магнитном поле // Дефектоскопия, 2002, №1. С.13-26.
4. Дубов А.А., Дубов Ал.А., Колокольников С.М. Метод магнитной памяти металла и приборы контроля: Учебное пособие. М.: ЗАО "Тиссо", 2008. 363 с.
5. Дубов А.А. Диагностика котельных труб с использованием магнитной памяти металла. М.: Энергоатомиздат, 1995. 112 с.
6. Дубов А.А., Дубов Ал.А., Колокольников С.М. Техническое диагностирование труб поверхностей нагрева паровых и водогрейных котлов с использованием магнитной памяти металла: Учебно-методическое пособие ИПК Госслужбы, 2006. 110 с.