Метрологические аспекты в методе магнитной памяти металла
д.т.н., профессор Дубов А.А.
В настоящее время все большее распространение на практике в России и в других странах получает метод магнитной памяти металла (МПМ). Принципиальные отличия метода МПМ от других магнитных методов НК представлены в статье [1]. Физические основы метода МПМ рассмотрены в работах [2 - 4]. На метод МПМ имеются российские и международные стандарты [5 - 7].
Согласно ГОСТ Р ИСО 24497-1-2009 [5] метод МПМ - метод неразрушающего контроля, основанный на регистрации и анализе распределения собственных магнитных полей рассеяния (СМПР), возникающих на изделиях и оборудовании в зонах концентрации напряжений (ЗКН).
ЗКН - это не только заранее известные области, где особенности конструкции создают различные условия для распределения напряжений, создаваемых внешней нагрузкой, но и случайно расположенные области, где в силу начальной неоднородности металла в сочетании с нерасчетными дополнительными рабочими нагрузками возникают большие деформации (как правило, деформации сдвига).
Контроль методом МПМ осуществляется без зачистки металла и искусственного намагничивания. Используется остаточная намагниченность, которая сложилась естественным образом при изготовлении изделий и в процессе их эксплуатации.
Плавка, ковка, штамповка, термическая обработка, сварка происходят при температуре, значительно превышающей точку Кюри металла (для сплавов на основе железа - порядка 760-770°С), когда исчезает остаточная намагниченность.
При последующем остывании металла в момент прохождения через точку Кюри (Tк), когда магнитная проницаемость µ максимальна, изделия приобретают высокий уровень термоостаточной намагниченности даже в слабом внешнем геомагнитном поле.
В результате этого процесса, при котором энергия кристаллизации и термических напряжений (наружные слои изделия охлаждаются быстрее внутренних) на порядок больше энергии слабого внешнего магнитного поля, распределение термоостаточной намагниченности в изделиях по величине и направлению определяется формой изделия, его структурной и технологической неоднородностью. Таким образом, структурная и технологическая наследственность металла, обусловленная процессом охлаждения, проявляется в виде естественной намагниченности (магнитной памяти металла).
Многочисленные исследования, выполненные разработчиками метода на заводах-изготовителях, показали, что практически все однотипные изделия, изготовленные из одной марки стали и по одной технологии, имеют одинаковое распределение остаточной намагниченности, и только в зонах концентрации остаточных напряжений и различных неоднородностей структуры на отдельных изделиях при контроле фиксируются магнитные аномалии [8].
В условиях эксплуатации под действием рабочих нагрузок термоостаточная намагниченность перераспределяется, и в ЗКН возникают магнитные аномалии, которые фиксируются в режиме экспресс-контроля с использованием специализированных сканирующих устройств и магнитометрических приборов.
Приборы магнитометрические "ИКН" (измерители концентрации напряжений), используемые в методе магнитной памяти металла для определения ЗКН, сертифицированы, имеют свидетельство об утверждении типа средств измерений Федерального агентства по техническому регулированию и метрологии. Приборы измеряют напряженность магнитного поля в А/м, а результаты этих измерений по специальным методикам преобразуются в диагностические параметры, характеризующие состояние объекта контроля (ОК). Приборы проходят ежегодную поверку на эталоне, аттестованном в установленном порядке.
Контроль изделий машиностроения и различного оборудования с использованием метода МПМ осуществляется приборами со специализированными датчиками путем сканирования вдоль поверхности изделия с фиксированием изменения СМПР.
Следует отметить очень важную особенность СМПР в методе МПМ - отображение внутренних реологических свойств материала изделий: силомоментных напряжений, реакцию на воздействие внешних сил и релаксацию одновременно с геометрическими смещениями в процессе деформирования [9].
Геометрическим признаком магнитных аномалий в распределении СМПР, характеризующим ЗКН, является расстояние между экстремальными значениями собственного магнитного поля, кратное типоразмеру изделия (толщине, ширине, диаметру).
Особые геометрические признаки СМПР, фиксируемые в ЗКН, являются очень важным метрологическим фактором в методе МПМ. Этот фактор позволяет при практической диагностике отличать полезный магнитный сигнал от ложного.
Метод МПМ может применяться на изделиях, изготовленных из ферро- и парамагнитных материалов. На каждое конкретное изделие (или узел, находящийся в конструкции) одного типоразмера, изготовленного из одного материала, составляется отдельная методика контроля.
Учитывая, что главная задача метода МПМ заключается в определении ЗКН, которые являются источниками всех видов повреждений (коррозия, усталость, ползучесть), разработаны диагностические параметры, позволяющие решать эту задачу.
Для количественной оценки уровня концентрации напряжений (источников повреждений) при сканировании вдоль поверхности ОК определяется градиент нормальной (Нy) и/или тангенциальной (Нх) составляющих СМПР:
K = |ΔH| / Δx, при Δx→0 K = dH / dx, (1)
где Δx - расстояние между соседними точками контроля.
В отдельных случаях при контроле напряженно-деформированного состояния (НДС) оборудования используется результирующее СМПР, рассчитанное по результатам измерений трех составляющих

и градиент |ΔH| / Δx.
Среди основных расчетных диагностических параметров в методе МПМ применяется параметр m, характеризующий предельную деформационную способность материала:
m = Кmax / Кcp, (2)
где Кmax и Кcp, соответственно, максимальное и среднее значения градиента поля, которые определяются при контроле методом МПМ однотипных узлов оборудования.
В ходе промышленных и лабораторных исследований на образцах установлено соотношение между предельными значениями магнитных и механических параметров:
mпр = Кmax / Кcp ≈ Кпр / Кв ≈ σпр / σв, (3)
где значения Кmax и Кcp, полученные в результате контроля однотипных узлов оборудования, соответствуют значениям Кпр и Кв, полученным в результате испытаний на растяжение образцов, изготовленных из той же марки стали, при достижении, соответственно, истинного предела прочности при разрушении σпр и условного предела прочности σв.
В экспериментальных исследованиях было установлено также, что, если фактический параметр mф ≥ mпр, то в этом случае в металле контролируемого узла оборудования возникает предельное (критическое) состояние, при котором образуется макротрещина. Физическое обоснование параметра mпр приведено в работах [3, 10].
Иллюстрацию соотношения (3) можно представить на примере результатов испытаний стального образца на растяжение с постоянной скоростью деформирования вплоть до его разрыва с одновременным измерением СМПР образца по методу МПМ.
На рис.1 представлена диаграмма σ-ε, совмещенная с графиком изменения суммарного приращения СМПР Ʃ|∆H|, полученные при деформации растяжением стального образца.
Рассчитаем на данном примере значение параметра m по соотношению (3) между магнитными и механическими характеристиками.
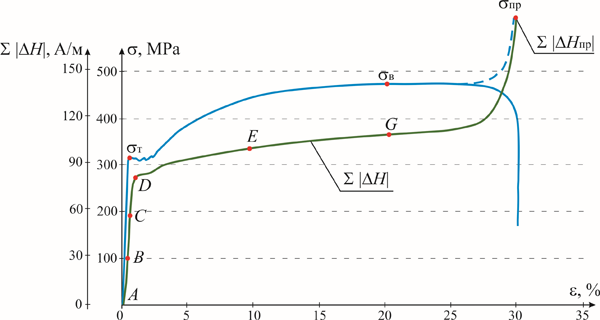
На участке диаграммы σ-ε от точки, соответствующей пределу прочности σв, до точки, соответствующей σпр, пунктирной линией показано изменение истинного напряжения по отношению к изменяющемуся сечению в шейке образца вплоть до предельного (разрушающего). Ниже на рис. 1 показана кривая приращений СМПР образца Σ|∆H|=ƒ(ε), соответствующая диаграмме σ-ε. Для данного образца значение σв, зафиксированное на диаграмме разрывной машины, равно 470 МПа, а расчетное напряжение σпр по отношению к площади конечного сечения в шейке оказалось равным 990 МПа.
Тогда значение параметра mпр для механических характеристик будет равно:
mпр = σпр / σв = 990МПА / 470МПА = 2,11, (4)
а значение параметра mпр для магнитных приращений равно:
mпр = Ʃ|∆Hпр| / Ʃ|∆Hв| = 214 / 106 = 2,02, (5)
где Ʃ|∆Hв| и Ʃ|∆Hпр| - суммарные приращения модульных значений СМПР, полученные при достижении, соответственно, условного предела прочности σв и истинного предела прочности σпр.
Таким образом, в результате данного эксперимента с растяжением стального образца получено хорошее подтверждение соотношения (3) между магнитными и механическими характеристиками. Аналогичное подтверждение соотношения (3) получено неоднократно, при испытании стальных образцов из материалов с кубической решеткой.
Соотношение (3) используется в методе МПМ для оценки предельного состояния металла реального оборудования, при котором в ЗКН образуется магистральная макротрещина, и начинается развитие повреждения.
Диагностический параметр m в методе МПМ является очень важным параметром в метрологическом смысле, т.к. он позволяет определять предельное состояние металла в ЗКН и момент начала трещинообразования.
Например, в методе акустической эмиссии (АЭ) оценка начала процесса трещинообразования до сих пор является проблемной задачей при контроле оборудования [11].
Здесь следует отметить, что раскрытие макротрещин при достижении предельного состояния металла составляет доли миллиметров, что является зоной нечувствительности для большинства методов НК. В этой связи, следует отметить также очень важную особенность метода МПМ, заключающуюся в том, что он позволяет по параметрам магнитных аномалий в ЗКН, где уже образовались макротрещины, оценивать степень их опасности, и делать выводы о направлении и интенсивности их развития.
Рассмотрим далее более подробно возможности метода МПМ решать указанную выше задачу с позиции метрологического обеспечения. Как было отмечено ранее, метод МПМ это, прежде всего, метод контроля фактического напряженно-деформированного состояния (НДС), основной задачей которого является определение ЗКН с геометрическими признаками распределения СМПР в этой зоне, обусловленными типоразмером данного ОК. В методе МПМ используется "безэталонный" способ контроля НДС, т. е. путем сравнения магнитных аномалий по амплитуде и ширине СМПР в ЗКН и вне этой зоны. Такое сравнение выполняется индивидуально для каждого ОК. Однако энергетическое соотношение между магнитными и механическими параметрами (3) для разных ОК, имеющих разные типоразмеры, но изготовленных из одного материала, является одинаковым. Данная закономерность установлена как в лабораторных испытаниях (рис. 1), так и в многочисленных практических работах. Соотношение (3) позволяет решить проблему "масштабного фактора" при переносе на реальное оборудование тарировочных зависимостей, полученных на образцах.
Одна из экспериментально установленных и используемых методиками МПМ зависимостей - это аппроксимация объективно существующей взаимосвязи предельных деформационных параметров в локальной области развивающегося повреждения со среднестатистическими деформационно-силовыми макро-характеристиками материала, полученными при испытании образцов [3, 4].
При этом принципиально важно, что поле рассеяния над аномальной областью формируется не каким-либо одним видом локальной деформации, а совокупностью всех видов локальной деформации, учитывающей не только их абсолютные величины, но и ориентационные соотношения в пространстве силового поля - совокупностью, определяющей локальную плотность собственной энергии материала, измененную внешним воздействием. В этом принципиальное отличие метода магнитной памяти от всех других методов диагностики НДС.
Выявленный магнитомеханический критерий оценки предельного состояния материала – отношение предельной величины плотности внутренней энергии материала к средней величине - нуждался в "переводе" на привычный "язык" при его использовании на практике. Этот «перевод», предложенный автором метода МПМ, выражается простой функцией:
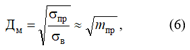
где Дм - коэффициент, вычисленный по измеренным параметрам поля рассеяния, определяемого совокупностью локальных деформаций в области появившейся макротрещины, эквивалентом которых, как можно теперь понять из полученных выше результатов, может служить средняя относительная продольная деформация (εн) в области неравномерного деформирования (в области "шейки"), т.е. Дм = εн. Этот коэффициент назван "предельным коэффициентом концентрации напряжений".
На рис. 2, а представлено распределение множества рассчитанных значений корня квадратного из отношения предельного значения удельной нагрузки к пределу временной прочности для разных материалов (табл. 1) в зависимости от соответствующих средних значений относительного удлинения в области неравномерной деформации образца [3]. Здесь же на рис. 2, а приведены две функции: полученная расчетом для всех 98 испытанных образцов и "точной аппроксимации" - пунктирная линия, и сплошная линия - функция "перевода" (6), используемая в методиках диагностики методом МПМ.
На рис. 2, б представлено распределение погрешностей аппроксимации выявленной закономерности в работе [3] с функцией "перевода".
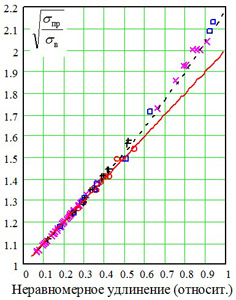
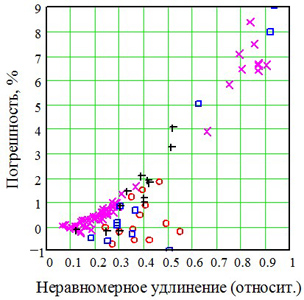
Рис.2. Одна из основных зависимостей, используемых в МПМ для оценки НДС разных материалов (сплошная линия) (а), потенциальная погрешность МПМ (б).
Таблица 1.
N | Тип сплавов | Характеристика группы образцов | Обозначение на графике | Количество образцов |
---|---|---|---|---|
Результаты испытаний |
||||
1. | Титановый сплав | одна марка | × - I | 22 |
2. | Рельсовая сталь | одна марка | × - II | 27 |
3. | Алюминиевый сплав | одна марка | × - III | 12 |
Справочные данные |
||||
4. | Ферромагнитные углеродистые стали | разные марки | ○ | 13 |
5. | Хромистые низко- и среднелегированные стали | разные марки | □ | 12 |
6. | Хромоникелевые сплавы | разные марки | + | 12 |
Общее количество образцов и марок |
98 |
В таблице 2 приведена статистика распределения рассматриваемой погрешности по группам сталей, указанным в табл. 1. По сути, это статистика потенциальной достоверности1) значений "предельного коэффициента концентрации напряжений", используемого в методиках диагностики методом МПМ.
1) Потенциальная достоверность - максимально возможная достоверность результатов, определяемая идеологией метода, т. е. адекватностью используемых аппроксимирующих функций реальным физическим закономерностям исследуемого процесса.
Как видим из табл. 2, это достаточно высокая достоверность результатов диагностики и оценки состояния материала при использовании метода МПМ (не менее 90%).
Таблица 2. Статистические характеристики потенциальной достоверности значений "предельного коэффициента концентрации напряжений", используемого в методе МПМ
Параметры разброса | Номер исследуемой группы сплавов | Для всех групп | |||
---|---|---|---|---|---|
1, 2, 3 | 4 | 5 | 6 | ||
Максимальные отклонения, % | -1,1 9,1 |
||||
Среднее отклонение, % | 1,5 | 0,3 | 1,8 | 1,4 | 1,4 |
Среднее квадратичное отклонение, % | 2,5 | 0,9 | 3,4 | 1,3 | 2,4 |
Необходимо отметить, что конфигурация потока индукции собственного магнитного поля рассеяния в локальной области металла с аномальными значениями деформаций на поверхности образца или диагностируемого объекта является неоднородной.
Поток индукции СМПР, обусловленный деформацией скольжения, имеет вид расходящегося веера, причем, ширина "пучка" векторов индукции на поверхности объекта определяется только размерами локальной области. Простая логика показывает, что для достижения максимальной разрешающей способности, определяемой размерами локальной области, необходимо уменьшать диаметр приемной "катушки" индуктивности.
Заметим, что в этом случае ничто, кроме чисто конструктивных возможностей, не ограничивает минимальный размер приемника. Правда, кроме конструктивных и технических трудностей изготовления приемников малого диаметра, существует "здравый смысл", основанный на многочисленных экспериментальных результатах, утверждающий, что "бесконечно" уменьшать диаметр приемника нет необходимости: уже при диаметре в 1 мм практически реализуется оптимальная разрешающая способность не более 10÷50 мкм, что позволяет регистрировать локальные аномалии, состояние материала в которых еще очень далеко от развития разрушения. Такой высокой разрешающей способностью не обладает ни один из известных неразрушающих методов диагностики напряженно-деформированного состояния материалов.
Метрологические граничные условия
На основе опыта применения метода МПМ и соответствующих приборов контроля выявлены погрешности, которые отнесены к метрологическим граничным условиям. Эти погрешности условно разделены на следующие группы:
- погрешности, возникающие при измерениях СМПР на объекте контроля в зависимости от типа датчика и его положения относительно поверхности;
- погрешности, связанные с отстройкой от влияния размагничивающего фактора;
- погрешности, связанные с искусственной намагниченностью от внешних источников;
- погрешности, обусловленные состоянием наружной поверхности объекта контроля (наличие изоляции, краски, окалины и т.д.);
- погрешности, зависящие от настройки и калибровки приборов контроля и внутренних приборных "шумов", обусловленных работой процессора и микросхем;
- случайные погрешности вследствие наклепа, трения соприкасающихся деталей и прочее.
В заключении необходимо отметить следующее. Рассмотренное в данной статье метрологическое обеспечение метода МПМ распространяется на область контроля НДС изделий машиностроения и оборудования до достижения предельного состояния металла (до момента трещинообразования) в локальных ЗКН. Для решения этой задачи перечисленные граничные условия не оказывают существенного влияния при определении расчетного параметра m , характеризующего состояние металла в ЗКН, т.к. этот параметр является относительным к фоновым значениям СМПР на ОК. Очень важными граничными условиями, которые необходимо учитывать при оценке состояния изделий или узлов, находящихся в конструкции, являются: одинаковость формы и типоразмера, технологии производства, марка стали (структурные и механические свойства металла), одинаковое расположение при контроле изделий или узлов относительно внешнего геомагнитного поля, одинаковые расчетные и рабочие параметры. Перечисленные граничные условия необходимо выполнять для определения однородных реологических полей [9] (в методе МПМ - это СМПР).
Метрологические граничные условия более существенное влияние оказывают при классификации параметров СМПР по видам и размерам развитых дефектов после превышения предельного состояния металла в ЗКН. Эти условия более подробно рассматриваются в специальных методиках. В настоящее время задача классификации по видам и размерам дефектов, как правило, решается при комплексном контроле в сочетании метода МПМ с другими методами НК. Методом МПМ в режиме экспресс-контроля определяются ЗКН - источники развивающихся дефектов, а затем в этих зонах выполняется дополнительный контроль, например, УК с классификацией дефектов по нормам УК. При таком комплексном подходе резко упрощается контроль и в то же время повышается его эффективность.
Литература
1. Дубов А.А. Принципиальные отличия метода магнитной памяти металла от других известных методов неразрушающего контроля. Итоги и перспективы развития // Территория NDT, 2016, № 2. С.64-68.
2. Власов В.Т., Дубов А.А. Физические основы метода магнитной памяти металла. М.: ЗАО "Тиссо", 2004. 424 с.
3. Власов В.Т., Дубов А.А. Физическая теория процесса "деформация-разрушение". Часть I. Физические критерии предельных состояний металла. М.: ЗАО "Тиссо", 2007. 517 с.
4. Власов В.Т., Дубов А.А. Физическая теория процесса "деформация-разрушение". Часть II. Термодинамика процесса. М.: Издательский дом "Спектр", 2016. 228 с.
5. ГОСТ Р ИСО 24497-1-2009. Контроль неразрушающий. Метод магнитной памяти металла. Часть 1. Термины и определения.
6. ГОСТ Р ИСО 24497-2-2009. Контроль неразрушающий. Метод магнитной памяти металла. Часть 2. Общие требования.
7. ГОСТ Р ИСО 24497-3-2009. Контроль неразрушающий. Метод магнитной памяти металла. Часть 3. Контроль сварных соединений.
8. Дубов А.А. Определение металлургических и технологических дефектов в изделиях машиностроения с использованием магнитной памяти металла // Металлург, 2015, № 2. С.62-65.
9. Гораздовский Т.Я. Научные основы реологии. Луганск: Всеукраинский Национальный университет, 2009. 699 с.
10. Дубов А.А., Дубов Ал.А., Колокольников С.М. Метод магнитной памяти металла и приборы контроля: учеб. пособие. 5-е изд. М.: Издательский дом "Спектр", 2012. 395 с.
11. Овчарук В.Н. Метрологические аспекты регистрации энергетических параметров акустической эмиссии материалов // Измерительная техника, 2014, № 8. С.57-61.