Проблемы контроля качества сварки и сварочных технологий и их решение на основе метода магнитной памяти металла
д.т.н., профессор Дубов А.А., Колокольников С.М.
Сварка существует в мире более 100 лет, однако до сих пор имеет место множество проблем, связанных с контролем качества сварных соединений изделий и обеспечением надежности сварных конструкций. Среди наиболее важных проблем следует отметить следующие:
- низкая эффективность традиционных средств и методов при контроле напряженно-деформированного состояния сварных соединений и определении зон концентрации напряжений - источников развития повреждений;
- отсутствие в широкой практике научно-обоснованных норм по допустимости размеров дефектов с позиций механики разрушений;
- коробление или изменение формы и размеров конструкции в результате неравномерного нагрева и охлаждения при сварке;
- отсутствие эффективных методов неразрушающего контроля (НК) качества термической и других технологий обработок сварных соединений с целью снятия остаточных напряжений;
- отсутствие эффективных методов НК точечной контактной сварки в изделиях машиностроения; до сих пор на практике контроль осуществляется на отрыв путем удара по месту точечной сварки молотком и зубилом;
- проблемной задачей является выбор оптимальных технологий сварки, наплавок, напылений;
- низкая эффективность традиционных методов НК при контроле контактной сварки труб, угловых, тавровых сварных соединений.
Одной из важных и сложных проблем современного неразрушающего контроля (НК) качества сварных соединений разных типов является поиск и определение в них "слабого звена" в единой комплексной системе факторов "структурно-механическая неоднородность - дефекты сварного шва - конструктивный и технологический концентратор напряжений", т.е. зон с высокой неоднородностью напряженно-деформированного состояния или зон концентрации напряжений (ЗКН). Это важно как при изготовлении сварных соединений, т.е. непосредственно после сварки, для оптимизации технологического процесса, так и при их эксплуатации.
Традиционная дефектоскопия, ориентированная только на поиск несплошностей в сварных соединениях, не может обеспечить достоверную оценку их качества. Опираясь только на результаты дефектоскопии технологу-сварщику трудно выявлять причины дефектности шва и совершенствовать технологию сварки.
В условиях, когда на надежность сварных соединений влияет множество факторов, необходим метод НК, который бы интегрально оценивал состояние металла сварного соединения.
В настоящее время в России разработан и успешно внедряется в различных отраслях промышленности принципиально новый метод диагностики металла изделий и сварных соединений, основанный на использовании магнитной памяти металла (МПМ).
Метод МПМ направлен на решение указанных выше проблем НК основного металла и сварных соединений объектов промышленности и транспорта.
МПМ - метод неразрушающего контроля, основанный на анализе распределения собственного магнитного поля рассеяния (СМПР) на поверхности изделий с целью определения зон концентрации напряжений, дефектов и неоднородности структуры металла и сварных соединений.
Путем считывания СМПР, отображающего остаточную намагниченность, сформировавшуюся естественным образом в процессе сварки, нам предоставляется уникальная возможность выполнять оценку фактического состояния сварного шва. Причем эта оценка является интегральной, отображающей в каждом шве одновременно особенности структурного состояния, распределение остаточных напряжений и дефектов сварки.
Формирование магнитной (доменной) структуры в сварных соединениях происходит одновременно с кристаллизацией при остывании металла в магнитном поле Земли и прохождении через точку Кюри (768°С) под действием напряжений и деформаций, возникающих в процессе сварки. На возникающих дефектах сварки образуются узлы закрепления доменных границ с выходом на поверхность сварного шва в виде СМПР. Таким образом, путем считывания СМПР, которые формируются в процессе сварки, нам предоставляется возможность выполнять интегральную оценку фактического состояния сварного шва.
Контроль методом МПМ осуществляется без зачистки металла и специального намагничивания и позволяет выполнять экспресс-контроль качества сварных соединений в ручном и автоматическом режиме и массовом производстве на различных изделиях из углеродистых, аустенитных и феррито-аустенитных марок сталей.
Контроль выполняется с помощью специализированных малогабаритных приборов, имеющих автономное питание, сканирующие и регистрирующие устройства. Приборы типа ИКН (измерители концентрации напряжений магнитометрические) не имеют аналогов, серийное их изготовление организовано в России на предприятии "Энергодиагностика" (г.Москва). Приборы аттестованы в Госстандарте РФ и включены в государственный реестр средств измерений.
На рис.1 представлена схема контроля стыковых сварных соединений труб. Как видно из рис.1, феррозондовые преобразователи 1 и 3 располагаются при контроле по зонам термического влияния (ЗТВ) с обеих сторон шва, преобразователь 2 расположен между ними посередине, а преобразователь 4 расположен вертикально в противоположную сторону и предназначен для отстройки от внешнего магнитного поля.
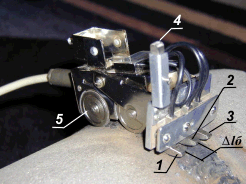
На рис.2,а показано типичное распределение остаточных напряжений на сварном соединении пластин. На рис.2,б показано распределение тангенциальной составляющей магнитного поля рассеяния Hpx, которое фиксируется при контроле МПМ при измерении поля перпендикулярно сварному шву (1, 2, 3 - разные сечения пластины). Из этих рисунков видна хорошая качественная сходимость распределений остаточных напряжений и магнитного поля.
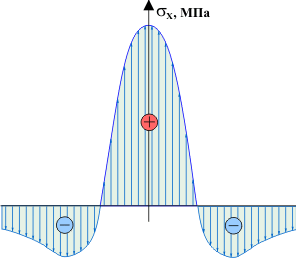
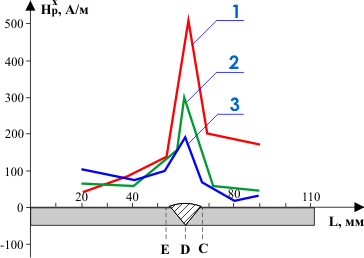
Известно, что оперативный контроль качества термической обработки сварных соединений, как правило, осуществляется только путем измерений твердости металла. Однако, такой точечный контроль не дает уверенности в отсутствии концентраторов механических напряжений по всему шву и в прилегающей к нему зоне.
Рассмотрим эффективность метода МПМ при контроле качества термической обработки сварного шва на отрезке трубы ⌀220х20 мм из низколегированной марки стали типа 12Х1МФ. Термообработка осуществлялась с нагревом металла шва от индукционной катушки до 700°С с последующим охлаждением на воздухе.
На рис.3 представлены магнитограммы, характеризующие напряженно-деформированное состояние отрезка трубы вдали от сварного шва (рис.3,а) и металла сварного шва, соответственно, до (рис.3,б) и после термической обработки (рис.3,в). Магнитограммы получены в результате измерений СМПР вдоль периметра трубы и сварного шва по схеме, представленной на рис.1. Из сравнения рис.3,б и рис.3,в видно, что магнитограмма, зарегистрированная на сварном шве после термической обработки, оказалась похожей на магнитограмму, которая была зарегистрирована в исходном состоянии на поверхности трубы вдали от сварного шва. Из представленного на рис.3 эксперимента следует вывод о том, что в качестве стандартного образца сравнения может быть использована магнитограмма, измеренная вдоль периметра трубы рядом со сварным соединением, где влияние сварки отсутствует.
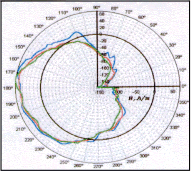
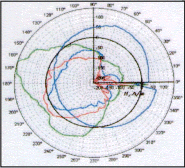
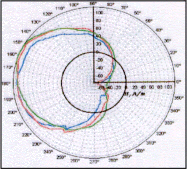
Рис.3. Магнитограммы, характеризующие напряженно-деформированное состояние отрезка труб вдали от сварного шва (а) и металла сварного шва до (б) и после (в) термической обработки.
На рис.4 представлены результаты измерения нормальной составляющей поля Hр, характеризующей распределение остаточных напряжений и деформаций после сварки двух одинаковых пластин. Пластины в процессе сварки были свободны и прогнулись немного вверх. Распределение поля Hр в рассматриваемом случае наглядно показывает влияние геометрических размеров пластин и их коробления на уровень и характер распределения остаточных сварочных деформаций и напряжений.
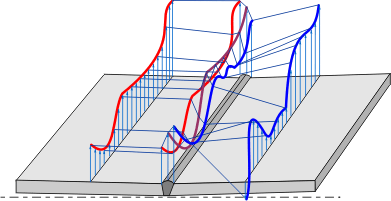
На рис.5,а показано распределение поля Hр на сварном соединении трубы, зафиксированное в зонах термического влияния шва (ЗТВ), и на рис.5,б - распределение остаточных напряжений, измеренное на сварном шве рентгеновским дифрактометром в этих же зонах.
Качество сварного соединения по методу МПМ оценивается по характеру распределения магнитного поля Hр и его градиента dHр/dx, где dx - минимальное расстояние между двумя соседними точками измерений поля Hр. Значение градиента определяется автоматически как модульная разность |ΔHр|, деленная на дискретное расстояние Δх между двумя соседними точками измерения, которое устанавливается при предварительной настройке прибора.
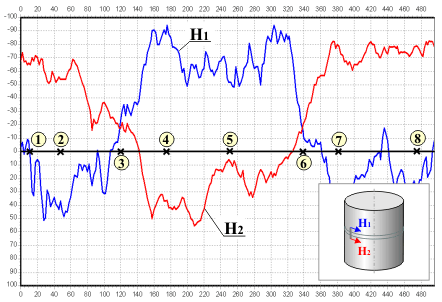
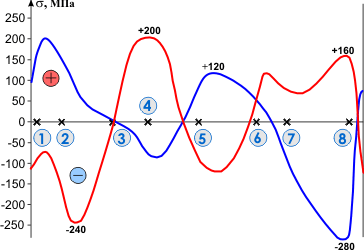
1...8 - точки измерения напряжений рентгеновским дифрактометром симметрично с двух сторон шва по ЗТВ;
--- результаты измерений напряжений, соответствующие полю H1;
--- результаты измерений напряжений, соответствующие полю H2.
На рис.6,а показано распределение нормальной составляющей поля Hp вдоль проконтролированного участка сварного шва нижнего днища реактора полимеризации предприятия "Anwil S.A." (г.Влоцлавек, Польша). На рисунке 6,б отмечено расположение выявленных трещин. В зонах выявленных трещин зафиксировано разнополярное распределение магнитного поля по каналам H1 и H2. Участок линии КН (Hр=0) (см. рис.6,б) с максимальным значением градиента dHр/dx располагается в ЗТВ шва и является продолжением выявленной трещины.
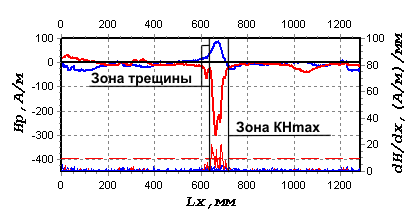
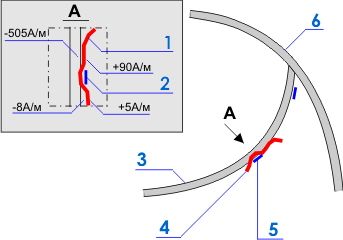
В результате контроля были сделаны следующие выводы и рекомендации:
- трещина является развивающимся дефектом в направлении максимальной ЗКН;
- выборку металла и наплавку следует проводить не только в зоне выявленной трещины, но и в зоне максимальной концентрации напряжений для предотвращения развития трещины в процессе эксплуатации.
Известно, что остаточная деформация металла сварного шва формируется в результате сдвиговой пластической деформации, происходящей при кристаллизации в процессе остывания металла. При этом диагностические параметры Hр и его градиент Кин (dHр/dx) вследствие "магнитодислокационного" гистерезиса, обусловленного двуединством магнитной плоскости и плоскости скольжения дислокаций, отображают распределение остаточных деформаций и напряжений вдоль периметра сварного соединения.
В работе [1] приведено соотношение между предельными значениями магнитных параметров mпр, Кинв, Кинт и механическими характеристиками металла σв, σт:
mпр = Кинв / Кинт ≈ (σв / σт)2, (1)
где mпр - магнитный показатель предельного деформационного упрочнения; Кинв и Кинт - значения градиентов поля, полученные при испытаниях образцов на растяжение, при достижении, соответственно, предела текучести σт и предела прочности σв.
Следует отметить, что соотношение (1), полученное в экспериментальных исследованиях, подтверждено расчетными исследованиями, представленными в работе [2], и обусловлено квадратичной зависимостью параметра Кин от магнитной и, соответственно, механической энергии, аккумулирующейся в металле ЗКН.
Методика определения градиента поля Кинв и Кинт в промышленных условиях изложена в работе [1]. Как правило, максимальное значение Кинmax, выявленное в отдельных ЗКН, соответствует Кинв, а среднее значение Кинср, рассчитанное для всех ЗКН, выявленных при контроле оборудования, приравнивается условно к значению Кинт.
Тогда соотношение (1) можно выразить:
mпр = Кинmax / Кинср ≈ (σmax / σср)2, (2)
где σmax и σср - соответственно, максимальное значение напряжения в ЗКН и среднее значение напряжений для всех ЗКН, выявленных при контроле.
Соотношения (1) и (2) получены в лабораторных и промышленных исследованиях для основного металла. Для сварных соединений эти соотношения следует использовать отдельно для ЗТВ и отдельно для локальных зон концентрации напряжений, обусловленных дефектами сварки (поры, шлаковые включения, непровары и т.д.).
Согласно [3], коэффициент концентрации напряжений для сварного соединения равен:
Кд ≈ σmax / σср, (3)
где σmax - максимальные напряжения в ЗКН; σср - среднее напряжение в сварном соединении.
В работе [3] дается оценка значений Кд:
- 2÷3 для пор;
- 3÷10 для шлаковых включений;
- 10÷100 для трещин, подрезов и непроваров в корне шва.
Очевидно, что соотношения (1) и (2) можно использовать и для локальных ЗКН, обусловленных дефектами сварки, с поправками на размеры дефектов и глубину их залегания.
Здесь важно отметить ошибочность в существующих подходах различных разработчиков средств контроля при оценке распределения остаточных напряжений в сварных соединениях. Как правило, по результатам контроля различными средствами (тензометрия и интерферометрия с рассверловкой металла, рентген, ультразвук, эффект Баркгаузена, метод магнитной анизотропии и другие) уровень остаточных напряжений на сварных швах не превышает предела текучести σт, что, как правило, не соответствует фактическому распределению напряжений.
Как показывает практика, уровень направленных остаточных напряжений (нормальных или тангенциальных) в ЗКН может достигать 1000 МПа и более. Этот уровень напряжений может иметь еще большие значения в зонах развивающихся дефектов сварки и трещин. Эти практические наблюдения убедительно подтверждают результаты контроля сварных соединений методом МПМ в ЗКН и вне ее в сочетании, например, с измерением твердости и пересчетом её результатов в единицы измерений напряжений. Например, уровень "контактных" напряжений, измеренных твердомерами МЭИ, в ЗКН, выявленных методом МПМ, нередко достигал 1500 МПа и более. Необходимо помнить, что деформации и напряжения являются объемными и имеют в каждой точке контроля, как минимум, три составляющие (радиальную и две тангенциальные).
Распределение СМПР в каждой "точке" контроля, измеренное трехкомпонентными датчиками с точностью до 1мм на поверхности металла сварного шва и в ЗТВ, в соответствии с имеющейся методикой напрямую отображает трехосное распределение остаточных напряжений и деформаций. При этом важно знать не уровень абсолютных напряжений (хотя эта задача в методе МПМ решена!), а их распределение по глубине и вдоль поверхности, и, самое главное, при этом не допустить предельного состояния металла перед образованием трещины.
В настоящее время в России метод магнитной памяти металла получил широкое развитие:
- разработано более 45 руководящих документов и методик контроля оборудования в различных отраслях промышленности;
- имеются ГОСТы России: ГОСТ Р ИСО 24497-1-2009 "Контроль неразрушающий. Метод магнитной памяти металла. Часть 1. Термины и определения"; ГОСТ Р ИСО 24497-2-2009 "Контроль неразрушающий. Метод магнитной памяти металла. Часть 2. Общие требования"; ГОСТ Р ИСО 24497-3-2009 "Контроль неразрушающий. Метод магнитной памяти металла. Часть 3. Контроль сварных соединений".
В 2007 году в результате положительного голосования среди 18 стран-членов МИСа и более 10 стран комитета ISO утвержден международный стандарт ISO 24497-1:2007(Е), 24497-2:2007(Е), 24497-3:2007(Е) по методу магнитной памяти металла.
Литература
1. Дубов А.А., Дубов Ал. Ан., Колокольников С.М. Метод магнитной памяти металла и приборы контроля. Учебное пособие. М.: ЗАО "ТИССО", 2008. 365с.
2. Власов В.Т., Дубов А.А. Физические основы метода магнитной памяти металла. М.: ЗАО "ТИССО", 2004. 424с.
3. Федоров С.А. Контроль качества сварных и паяных соединений. Учебное пособие. М.: МАТИ, 1989.