Исследование статических и циклических деформаций с использованием метода магнитной памяти металла
Член-корреспондент РАН Махутов Н.Р. (Институт машиноведения РАН)
д.т.н., профессор Дубов А.А., Денисов А.С. (ООО "Энергодиагностика")
Отдельные результаты исследований механических и физических свойств стальных образцов с использованием эффекта магнитной памяти металла впервые были представлены в работах [1, 2].
Указанные исследования выполнялись в основном в условиях статических нагрузок растяжения. Отдельные фрагменты исследований стальных образцов в условиях циклической нагрузки растяжения с использованием метода магнитной памяти металла (МПМ) представлены в работе [3].
Проведение испытаний стальных образцов на статическую и циклическую нагрузку с использованием метода МПМ обусловлено необходимостью экспериментальной проверки корреляционной связи диагностических параметров метода с деформацией. Необходимость проведения таких испытаний с использованием метода МПМ также обусловлена существующими недостатками, которые имеют место в практике проведения испытаний образцов на циклическую прочность.
Это, во-первых, сложность обеспечения непрерывной записи диаграммы деформирования синхронно с амплитудой и частотой нагрузки за весь период приложения циклической нагрузки вплоть до разрушения образца. Для регистрации диаграмм циклического деформирования в процессе нагружения, как правило, переходят на более низкие частоты с целью обеспечения точности записи параметров нагружения.
Во-вторых, отсутствие физических методов экспериментальных исследований, позволяющих в режиме реального времени в процессе циклического нагружения синхронно, с частотой нагрузки, отслеживать физические процессы сопротивления деформированию, происходящие в металле образцов.
В последние годы делаются попытки использовать для этой цели метод акустической эмиссии (АЭ). Однако, невозможность установки датчиков АЭ непосредственно в зону предполагаемого разрушения образца, наличие посторонних шумов от работы испытательной машины затрудняют исследования АЭ в таких испытаниях.
Первые попытки использовать для этой цели метод МПМ и соответствующие приборы контроля, представленные в работе [3] показали хорошие результаты. Малогабаритные датчики приборов, используемые в методе МПМ, позволяют устанавливать их непосредственно вблизи места предполагаемого разрушения (с точностью до 1мм). При этом непосредственного контакта датчика с поверхностью образца не требуется в отличие от датчиков АЭ. Кроме того, использование двух- и трехкомпонентных датчиков позволяет, в силу магнитомеханического эффекта, следить за изменением амплитуды деформации в трех направлениях: в продольном (соосно с направлением внутренней нагрузки), в поперечном (перпендикулярно приложенной нагрузке) и в радиальном направлении. При этом в режиме "таймера" с помощью специализированных приборов ИКН (измерителей концентрации напряжений), имеющих экран и блок памяти от 32 Мб и более, обеспечивается постоянное наблюдение за процессом циклического деформирования образца и оперативная запись результатов измерений магнитных параметров синхронно с приложенной циклической нагрузкой в широком диапазоне изменения частот (от 1 Гц до 300 Гц и более).
На рис.1 представлена схема измерений нормальной и тангенциальной (вдоль направления приложенной нагрузки Р) составляющих собственного магнитного поля образца, установленного в разрывную машину. Образец 2, имеющий специальную проточку 3 для локализации зоны контроля, устанавливался в узел крепления 1 разрывной машины на двух болтовых соединениях. Двухкомпонентный датчик 4, позволяющий измерить тангенциальную Нx и нормальную Нy составляющие магнитного поля вблизи поверхности образца (на расстоянии 0,5÷1,0мм), устанавливался в штатив 6 и закреплялся в нем жестко в одном положении. Электронный блок 5 - аналого-цифровой преобразователь - подключался к регистрирующему прибору ИКН.
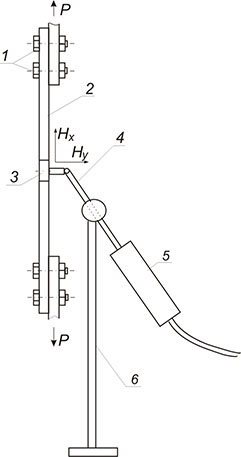
Далее рассмотрим отдельные результаты исследований стальных образцов при приложении циклической нагрузки растяжения в диапазоне от 1 до 10 Гц. Испытания образцов со схемой измерений, представленной на рис.1, выполнялись в Институте Машиноведения имени А.А Благонравова РАН на испытательной машине "Material Test System (MTS) 311.21".
На рис.2 представлена форма и размеры стальных образцов, используемых при испытаниях на циклическую нагрузку растяжения. В середине образцов было выполнено сужение сечения с целью определения места предполагаемого разрушения и максимального деформирования образца (ЗКН) и, соответственно, с целью определения места установки датчика прибора ИКН. Отверстия Ø 6 мм на захватах образца были сделаны под болтовые соединения с захватами, установленными в испытательной машине. Испытывались образцы двух типов:
- тип I, материал – конструкционная сталь 10ХСНД, предел текучести σт=450 МПа, предел прочности σв=570 МПа, площадь поперечного сечения F=5,5×4=22 мм2;
- тип II, материал – сталь 3, предел текучести σт=250 МПа, предел прочности σв=350 МПа, площадь поперечного сечения F=6,5×1,5=9,75 мм2.
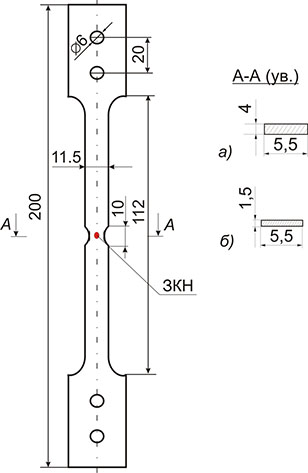
Всего было испытано четыре образца типа I и пять образцов типа II. Предварительно, с целью определения фактических значений σт и σв, было испытано по одному образцу каждого типа на статическую нагрузку растяжения. При этом производилась запись (в режиме реального времени приложения растягивающей нагрузки) одновременно диаграммы деформирования на регистраторе испытательной машины и изменения нормальной (ΔНy) и тангенциальной (ΔНх) составляющих магнитного поля в ЗКН образца.
На рис.3 и рис.4 представлено сопоставление диаграммы деформирования σ-ε и диаграммы изменения тангенциальной составляющей магнитного поля ΔНх в зависимости от напряжений растяжения, соответственно, для образца типа I и образца типа II.
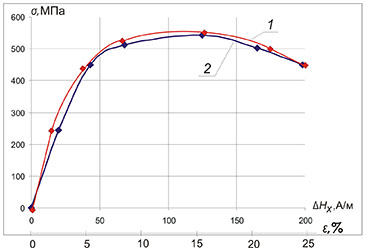
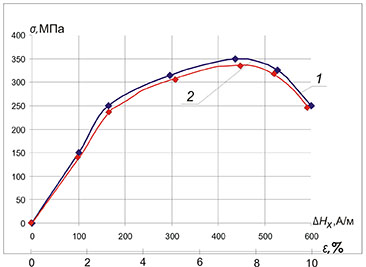
Из рис.3 и рис.4 видна хорошая корреляция между полученными диаграммами, которая подтверждает пропорциональную зависимость изменения собственного магнитного поля образца ΔНх от деформации растяжения на физическом уровне.
На рис.5 и рис.6 показаны изменения магнитного поля ΔНх в зависимости от деформации ε, полученные по результатам измерений в ЗКН (зоне шейки), соответственно, для образцов типа I и типа II. Видно, что зависимость ΔHx=f(ε) имеет линейный и пропорциональный характер.
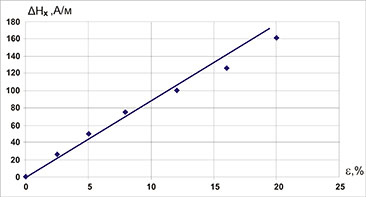
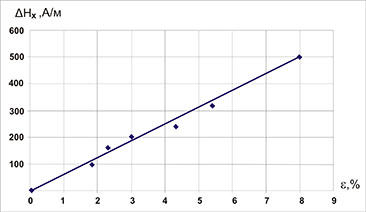
Далее были проведены испытания трех образцов (№2, №3, №4) типа I и четырех образцов (№2, №3, №4, №5) типа I на циклическую нагрузку растяжения с различной частотой.
Образцы типа I испытывались при диапазоне нагрузки растяжения от Pmin=100 кг до Pmax=950 кг или (0,2÷0,95)σт.
Образцы типа II испытывались при диапазоне нагрузки растяжения от Pmin=50 кг до Pmax=250 кг или (0,2÷1,0)σт.
На рис.7 и рис.8 приведены временные зависимости нормальной Hy и тангенциальной Hx составляющих магнитного поля от циклической нагрузки, полученные при испытании, соответственно, для образца №3 типа I (частота 2 Гц) и для образца №4 типа I (частота 10 Гц).
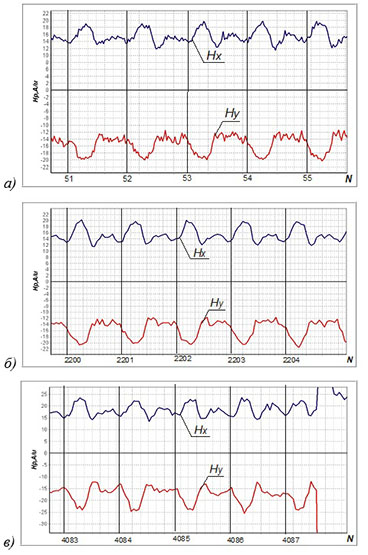
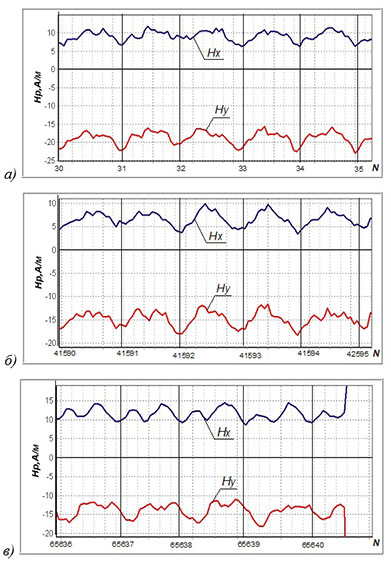
Общие закономерности, которые можно отметить из анализа магнитограмм, представленных на рис.7 и рис.8:
- совпадение по частоте приложенной нагрузки и амплитудного изменения составляющих поля Hy и Hx;
- незначительное амплитудное изменение значений составляющих поля Hy и Hx от амплитуды приложенной нагрузки на всех этапах циклов нагружения N вплоть до разрушения образцов;
- с увеличением частоты приложенной нагрузки с 2 Гц до 10 Гц значительно увеличивается число циклов до разрушения образца.
На рис.9 приведена временная зависимость тангенциальной составляющей магнитного поля Hх от циклической нагрузки растяжения, полученная при испытании образца №2 типа II на разных этапах циклического деформирования вплоть до разрушения. Из приведенных на рис.9 магнитограмм можно выделить следующие особенности:
- заметное увеличение амплитудного изменения составляющей поля Hх с увеличением числа циклов нагрузки N (на начальном этапе модульное изменение |ΔHх|≈150 А/м, в установившемся режиме |ΔHх|≈200 А/м и на конечном этапе |ΔHх|≈350 А/м);
- на максимуме приложенной нагрузки Pmax каждого цикла зафиксирован эффект резкого падения и мгновенного роста поля Hх. На минимуме амплитуды циклической нагрузки Pmin указанный эффект не наблюдается. Указанный эффект наблюдается для обеих составляющих поля Hу и Hх, как для образцов типа II, так и для образцов типа I (см. рис.7 и рис.8).
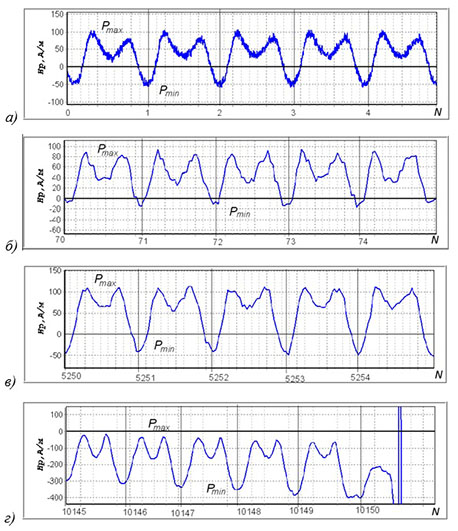
Следует отметить, что проявление эффекта кратковременного падения и роста составляющих поля Hу и Hх на максимуме циклической нагрузки растяжения постепенно увеличивается по мере увеличения числа циклов и достигает максимального значения по амплитуде непосредственно перед разрушением образца. На образцах типа II (сталь 3) амплитуда изменения составляющих поля Hу и Hх заметно больше по сравнению с образцами типа I (сталь10ХСНД).
На рис.10 представлена диаграмма циклического деформирования σ-ε, зафиксированная на образце №2 типа II циклического нагружения растяжением в диапазоне (0,2÷1,0)σт. При данной диаграмме частота приложения нагрузки была снижена с 3 Гц до 1 Гц и менее. Из сравнения рис.10 и рис.9 видно, что на диаграмме σ-ε эффект кратковременного роста и падения сопротивления деформированию на максимуме приложенной нагрузки не наблюдается.
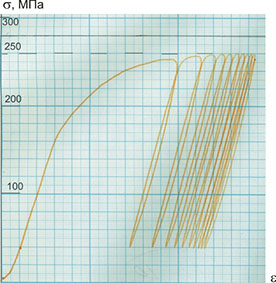
Однако, общий характер кривой σ-ε (ширина петли) на максимуме нагрузки соответствует магнитограмме, представленной на рис.9. На минимуме циклической нагрузки вид диаграммы σ-ε практически соответствует магнитограмме, представленной на рис.9.
На рис.11 и рис.12 представлено изменение тангенциальной составляющей магнитного поля ΔHх в зависимости от числа циклов нагружения N, зафиксированное при испытании, соответственно, образца №4 типа Ι и образца №2 типа ΙΙ.
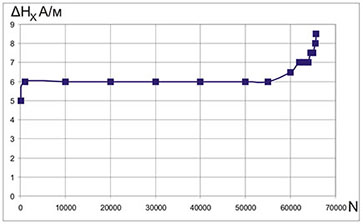
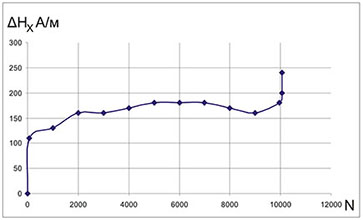
В соответствии с закономерностями, установленными в работе [4], кривые ΔHх=f(N), представленные на рис.11 и рис.12, качественно соответствуют кривым усталости металла образцов.
По этим кривым предоставляется уникальная возможность выполнять оценку развития процесса усталостного разрушения образцов во времени в зависимости от числа циклов, частоты и амплитуды нагрузки. Следует отметить, что оценка ресурса оборудования с использованием диагностических параметров метода МПМ (изменение магнитного поля ΔНр и его градиента ΔНр/Δх в ЗКН) в настоящее время успешно используется на практике.
Анализ результатов и выводы
1. Полученные результаты исследований образцов экспериментально подтвердили сделанный ранее вывод о возможности применения метода МПМ и соответствующих приборов контроля для экспресс-испытаний механических свойств и параметров циклической прочности на физическом уровне.
2. Сопоставление диаграмм деформирования σ-ε и магнитограмм σ-ΔНх, ΔHх-ε, полученных в режиме статического нагружения (см. рис.3, рис.4, рис.5, рис.6), диаграмм циклического нагружения σ-ε (см. рис.10) и соответствующих магнитограмм (см. рис.7, 8, 9) еще раз подтверждает установленную ранее связь магнитомеханических параметров, обусловленную "магнитодислокационным гистерезисом".
3. В процессе циклического нагружения установлена линейная зависимость между амплитудой сопротивления деформированию Δε и амплитудой изменения собственного магнитного поля ΔH металла образца.
4. На максимуме приложенной нагрузки растяжения каждого цикла по параметрам магнитной памяти металла впервые зафиксирован эффект резкого падения и мгновенного роста сопротивления деформированию. На минимуме амплитуды циклической нагрузки растяжения указанный эффект не наблюдается. Проявление эффекта кратковременного изменения сопротивления деформированию на максимуме амплитуды циклической нагрузки растяжения постепенно увеличивается по мере увеличения числа циклов и достигает максимального значения по амплитуде между падением и ростом сопротивления деформированию непосредственно перед разрушением образца. На основании выполненных ранее экспериментальных исследований [2] можно предположить, что выявленный эффект характеризует накопление поврежденности металла в виде скопления и постепенного увеличения плотности дислокаций в ЗКН – месте потенциального разрушения образца.
5. Кривые усталости, построенные по изменению собственного магнитного поля образцов в процессе циклического нагружения, экспериментально подтверждают возможность оценки ресурса оборудования по параметрам магнитной памяти металла.
6. Магнитограммы, зафиксированные в процессе циклического нагружения образцов в режиме реального времени, позволяют заявить о возможности использования метода МПМ и приборов типа ИКН для мониторинга технического состояния непосредственно в процессе эксплуатации оборудования под нагрузкой. Учитывая, что на диагностические параметры метода МПМ не оказывают влияния различного рода шумы, и при использовании этого метода не требуется специального дополнительного нагружения, приборы типа ИКН и соответствующие датчики (не требующие непосредственного контакта с объектом контроля) имеют очевидные преимущества перед приборами АЭ, широко используемыми на практике для мониторинга технического состояния оборудования.
Литература
1. Дубов А.А. Исследование свойств металла с использованием эффекта магнитной памяти металла // Металловедение и термическая обработка металлов. 1997. №9.
2. Горицкий В.М., Дубов А.А., Демин Е.А. Исследование структурной поврежденности стальных образцов с использованием метода магнитной памяти металла // Контроль. Диагностика. 2000. №7.
3. Дубов А.А., Дубов Ал.А., Колокольников С.М. Метод магнитной памяти металла и приборы контроля: Учебное пособие. М.: ЗАО "ТИССО", 2008. 365 с.
4. Власов В.Т., Дубов А.А. Физические основы метода магнитной памяти металла. М.: ЗАО "ТИССО", 2004. 424 с.