Проблемы контроля напряженно-деформированного состояния нефтегазопроводов и их решение с использованием метода магнитной памяти металла
д.т.н. Дубов А.А., к.т.н. Дубов Ал.А.
С 1 января 2017 года вступил в силу приказ Ростехнадзора от 28 июля 2016 года № 316, которым внесены изменения в Федеральные нормы и правила в области промышленной безопасности "Правила проведения экспертизы промышленной безопасности", утвержденные приказом Ростехнадзора от 14 ноября 2013 года № 538 (далее "Правила").
В соответствии с указанными Правилами при проведении экспертизы технических устройств установлена необходимость контроля (изучения) их напряженно-деформированного состояния (НДС).
Проблемой контроля механических напряжений в работающих конструкциях и трубопроводах с целью оценки их состояния в настоящее время занимаются все ведущие диагностические центры мира. Однако до сих пор эффективных методов контроля напряжений, пригодных для практики, не было предложено.
Анализ возможностей известных методов контроля напряжений и деформаций в основном металле изделий и сварных соединениях оборудования и конструкций позволяет назвать их существенные недостатки. Основными недостатками являются:
- невозможность использования большинства методов в области пластической деформации;
- локальность контроля, их непригодность для контроля протяженных трубопроводов и крупногабаритных объектов;
- не учитывается неоднородность структуры металла и наличие остаточных напряжений;
- контроль выполняется, как правило, только на поверхности изделий из-за существующих проблем оценки глубинных слоев металла и металла сварных соединений;
- требуется построение градуировочных графиков на предварительно изготовленных образцах, которые не отражают фактическое НДС оборудования;
- требуется подготовка контролируемой поверхности и объектов контроля (зачистка, активное намагничивание, клейка датчиков и прочее);
- сложность определения положения датчиков контроля по отношению к месту и направлению действия максимальных напряжений и деформаций, определяющих надежность оборудования и конструкции.
Известно, что основными источниками повреждений трубопроводов являются зоны концентрации напряжений (ЗКН), в которых процессы коррозии, усталости и ползучести протекают наиболее интенсивно. ЗКН – это не только заранее известные области, где конструктивные особенности трубопровода создают различные условия для распределения напряжений, создаваемых внешней нагрузкой, но и случайно расположенные области, где в силу начальной неоднородности металла, в сочетании с нерасчетными дополнительными рабочими нагрузками, возникают большие деформации (как правило, деформации сдвига). Именно в ЗКН необходимо исследовать в первую очередь структурно-механические свойства металла.
Известные методы неразрушающего контроля напряжений (рентген, ультразвук (УК), шумы Баркгаузена, тензометрирование и другие) не позволяют решить эту сложную задачу – определение фактического НДС протяженных нефтегазопроводов с выявлением ЗКН, обусловленных действием рабочих нагрузок.
Кроме того, традиционные методы и средства НК напряжений, которые основаны на активном взаимодействии сигнала прибора с металлом трубопроводов, получают косвенную информацию об их напряженном состоянии, т.е. имеют недостаточную информативность физических полей, используемых при контроле. Любое искусственно вводимое от прибора физическое поле в объект контроля, находящийся в напряженно-деформированном состоянии (даже после снятия рабочих нагрузок), обязательно будет взаимодействовать с собственными физическими полями материала (например, электромагнитными), сформировавшимися на уровне кристаллической решетки. Вводимое в исследуемый материал поле, взаимодействуя с собственными полями материала, меняет его свойства и характеристики НДС объекта контроля. При этом характер, величина и время жизни изменений определяются динамическим соотношением энергий взаимодействующих полей. На практике, при проведении диагностики такие изменения просто не учитывают. Не учитывать фактическое энергетическое состояние объекта контроля (об этом свидетельствует, например, магнитная память металла) – грубейшая ошибка для всех методов контроля НДС! Особенно это относится к ЗКН, которые сосредоточены, как правило, на глубине и в объеме, и на поверхность трубопровода выходят в виде линий скольжения (мест образования трещин!) шириной до нескольких микрон. В данных объективных условиях большинство методов контроля напряжений оказывается неэффективными для оценки фактического НДС трубопровода, как по своей физической сущности, так и по метрологическим условиям (локальность в зоне максимальной концентрации напряжений – зоне зарождения трещины – составляет доли миллиметра, а размеры датчиков приборов, как правило, значительно превышают такую локальность). И главное – неизвестно, где и как ставить датчик, когда в общем случае не известны места образования зон максимальных напряжений (рабочих или остаточных).
Таким образом, перечисленные выше недостатки известных методов контроля НДС обусловлены физической сущностью этих методов и являются закономерными. Отсутствие метрологической базы для сертификации и поверки средств измерений характеристик НДС материалов (до сих пор в России и других странах нет единых эталонов и образцов) приводят к неоднозначности требований и ошибочности методического подхода к разрабатываемым средствам контроля. Более того, многие специалисты, использующие различные методы и средства контроля напряжений, выказывают уверенность в том, что они «измеряют напряжения», забывая о том, что измерить можно только деформацию, а напряжения рассчитывают по алгоритму тарировочной характеристики σ = f(ε), заложенной в процессор прибора.
Тарировку средств и методик контроля напряжений осуществляют на образцах при их растяжении статической нагрузкой на разрывной машине и, как правило, в упругой области деформации. В то же время известно, что реальные трубопроводы работают не только в условиях статической, но и циклической нагрузки, а развитие повреждений происходит в ЗКН, в которых металл работает в области пластической деформации. Более того, фактическое НДС трубопровода во многих случаях не соответствует расчетному НДС и в общем случае не известно фактическое распределение деформаций и напряжений по величине, знаку, направлению, глубине металла.
Перечисленные проблемы, возникающие на практике при контроле напряжений, не могут быть разрешены в рамках сложившихся представлений о внутренних напряжениях. В работе [1] впервые дано теоретически обоснованное и экспериментально подтвержденное новое понятие о внутренних напряжениях, как интегральной характеристики энергетического состояния металла в объеме реального изделия. В этой работе [1] также показано, что выполнение тарировки средств и методик контроля напряжений на образцах путем обычных испытаний на растяжение является принципиальной ошибкой. Показано, что переносить полученные тарировочные характеристики на реальное оборудование принципиально нельзя, как в силу масштабного фактора, так и по физическим основам. При этом идеологическим фундаментом для развития темы «Контроль напряжений» должна быть энергетическая концепция, отображающая объективные процессы перераспределения собственной энергии материала, как реакции на внешнее воздействие. В этой связи, в работе [2] представлены новые требования к методам и средствам диагностики напряженно-деформированного состояния.
Здесь следует отметить, что метод магнитной памяти металла (МПМ) – это первый метод диагностики энергетического состояния материала (энергодиагностика).
Метод МПМ не требует подготовительных работ (зачистки поверхности, снятия изоляции, искусственного намагничивания). При контроле НДС протяженных участков трубопроводов используется связь собственного магнитного поля рассеяния (СМПР) с фактической деформацией. На метод МПМ имеются российские и международные стандарты [3, 4, 5].
Экспериментальные исследования и практические результаты применения метода магнитной памяти металла послужили основой для разработки идеологически нового энергетического подхода к оценке напряженно-деформированного состояния оборудования и конструкций.
В основе энергетического подхода лежит идея о том, что каждое изделие определенной формы и материала имеет определенную энергоемкость, характеризующую его определенную сопротивляемость внешним нагрузкам и разрушению. В экспериментальных исследованиях было получено, что предельное состояние, наступающее при разрушении изделия (или какого-либо участка трубопровода), имеет одинаковую энергетическую характеристику, т.е. энергия разрушения изделия независимо от различного сочетания факторов и физических эффектов, приведших его к этому состоянию, одна и та же и является энергетической константой. При этом время достижения предельного состояния даже для однотипных изделий, в зависимости от различного сочетания факторов, может быть разным. На основе энергетического соотношения между магнитными и механическими параметрами, полученного при испытании образцов на статическую и циклическую нагрузку с использованием метода МПМ, перенос тарировочных значений СМПР с образцов на реальное оборудование становится возможным [6.7].
В настоящее время при оценке фактического НДС нефтегазопроводов, расположенных под слоем грунта, все большее применение на практике получает бесконтактная магнитометрическая диагностика (БМД) [8]. БМД основана на измерении искажений магнитного поля Земли вдоль трассы нефтегазопровода, обусловленных изменением намагниченности металла труб в ЗКН и в зонах развивающихся повреждений.
При БМД трубопроводов используются магнитные параметры, которые разработаны в методе МПМ. В частности, при БМД, также как и в методе МПМ, выявлена четкая связь между периодичностью изменения всех трех составляющих измеряемого СМПР и типоразмером контролируемой трубы (диаметром, толщиной стенки и длиной труб между стыками). Эти качественные диагностические параметры характеризуют в макро-объеме металла трубы ЗКН – источники развития различного вида повреждений.
В настоящее время при прокладке нефтегазопроводов в северных районах России с целью снижения коррозионного износа все большее применение находят трубопроводы в пенополиуретановой (ППУ) изоляции. Однако на трубопроводах в ППУ-изоляции, из-за меньшей потери тепла от металла трубы по сравнению с обычной изоляцией, перемещения трубы при самокомпенсации больше, и, соответственно, уровень напряжений в зонах их концентрации больше. При значительных колебаниях температуры наружного воздуха из-за недостатка самокомпенсации на отдельных подземных участках нефтегазопроводов возникает их повышенная деформация с выходом на поверхность грунта. «Выдавливание» на поверхность грунта подземных участков нефтегазопроводов в болотистых районах в зимнее время имеет место и на трубопроводах в типовой изоляции. На этих участках образуется высокая концентрация напряжений в основном металле и на монтажных стыках с развитием в них повреждений.
Эффективность БМД для оценки фактического НДС участков нефтегазопроводов, выдавленных на поверхность грунта, рассмотрим на следующем примере. В ноябре 2016 –январе 2017 года специалистами ООО "Энергодиагностика" на одном из дочерних предприятий ПАО "НОВАТЭК" был выполнен контроль 45 участков нефтепроводов ⌀ 377 × 10 мм в ППУ-изоляции в местах их выхода из под грунта на поверхность из-за повышенной нескомпенсированной деформации.
На рис.1, а представлен внешний вид одного из таких участков.
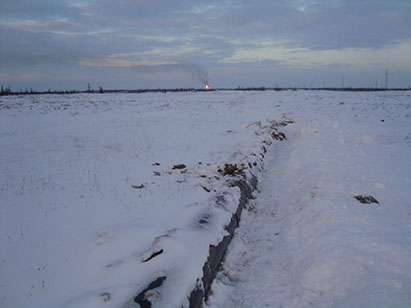
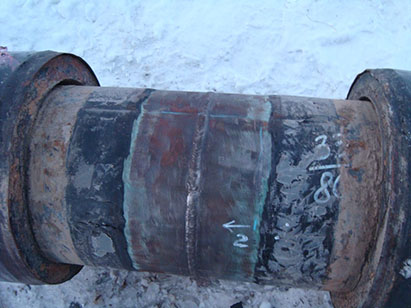
Рис.1. Участок нефтепровода с повышенной нескомпенсированной деформацией: а – внешний вид участка; б - монтажный сварной шов в зоне его вскрытия.
Запись магнитограмм при БМД выполнена магнитометрическим прибором – измерителем концентрации напряжений ИКН-6М-8 в комплекте со специализированным сканирующим устройством (СУ) Тип 11-6К. При движении оператора вдоль трассы нефтепровода проводилась запись магнитограмм с разбивкой по файлам. Начальная и конечная точки файла, а также все промежуточные точки отмечались по месту с последующей фиксацией их в системе GPS-координат. На рис.2 представлен приборный комплекс для БМД, изготавливаемый серийно предприятием "Энергодиагностика".
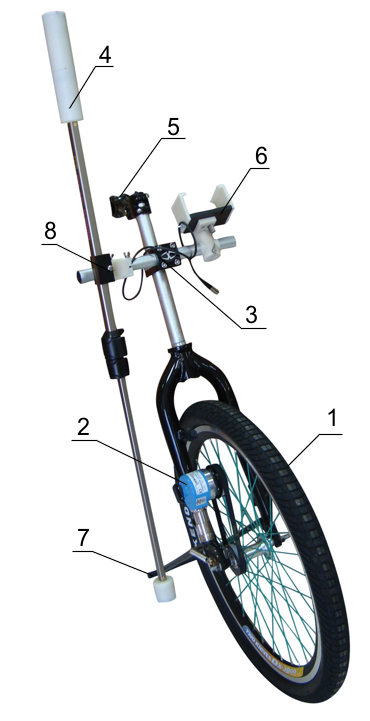
На рис.3, а представлена схема трассировки нефтепроводов ⌀ 377 × 10 мм на участке ПК 59+60, а на рис.3, б - магнитограмма, зафиксированная при БМД данного участка.
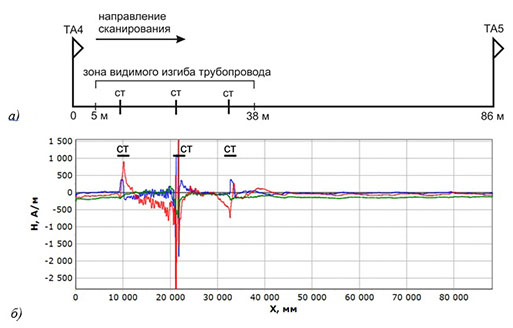
Из сопоставления рис.3, а и рис.3, б видно, что в зоне видимого изгиба нефтепровода и выхода его на поверхность грунта (рис.1) при выполнении БМД зафиксированы резкие локальные изменения собственного магнитного поля рассеяния (СМПР) нефтепровода. При этом максимальные изменения СМПР совпадают с местами расположения монтажных кольцевых стыков.
На втором монтажном стыке с максимальным изменением поля H после снятия изоляции (защитных кожухов) был выполнен дополнительный контроль методом МПМ (контактным способом) и УК (ультразвуковой контроль). На рис.1, б представлен монтажный сварной шов в зоне его вскрытия, а на рис.4 показаны результаты контроля этого шва методом МПМ с обозначением выявленных зон концентрации напряжений ЗКН1 и ЗКН2.
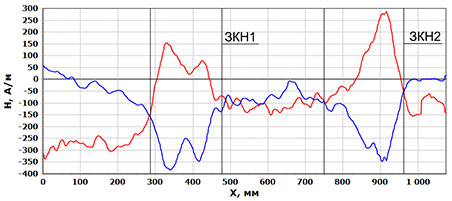
При ультразвуковом контроле данного сварного соединения в ЗКН1 и ЗКН2 были обнаружены недопустимые дефекты в виде протяженных несплошностей на глубине от 2 до 7 мм. Дефекты располагались в зоне термического влияния сварки со стороны максимальной пластической деформации прилегающего участка трубопровода. Данный монтажный стык было рекомендовано заменить.
Аналогичным образом методами БМД и МПМ были проконтролированы еще 44 участка с видимой деформацией нефтепровода общей протяженностью около 5 км. Выявлено 20 магнитных аномалий, характеризующих ЗКН с максимальной деформацией вблизи монтажных стыков. Практически все магнитные аномалии со значительным изменением собственного магнитного поля H трубопровода совпадали с местами расположения поперечных (кольцевых) сварных соединений.
Представленный пример выполнения контроля фактического НДС протяженных участков нефтепроводов с использованием БМД, метода МПМ и ультразвука убедительно показывает эффективность такого комплексного контроля. Очевидно, что оценка фактического НДС нефтепроводов с выявлением наиболее напряженных участков, расположенных в болотистых и труднопроходимых местах, с использованием расчетных методов и известных методов НК НДС (рентген, ультразвук (УК), шумы Баркгаузена, тензометрирование и другие), относящихся к лабораторным методам исследования, в таких условиях невозможна.
Литература
1. Власов В.Т., Дубов А.А. Физическая теория процесса "деформация - разрушение". Ч.I. Физические критерии предельных состояний металла. М.:ЗАО "Тиссо", 2007. 517 с.
2. Дубов А.А. Новые требования к методам и средствам диагностики напряженно-деформированного состояния материалов // Мир измерений, 2012, № 6. С.38-42.
3. ГОСТ Р ИСО 24497-1-2009. Контроль неразрушающий. Метод магнитной памяти металла. Часть 1. Термины и определения.
4. ГОСТ Р ИСО 24497-2-2009. Контроль неразрушающий. Метод магнитной памяти металла. Часть 2. Общие положения.
5. ГОСТ Р ИСО 24497-3-2009. Контроль неразрушающий. Метод магнитной памяти металла. Часть 3. Контроль сварных соединений.
6. Махутов Н.А., Дубов А.А., Денисов А.С. Исследование статистических и циклических деформаций с использованием метода магнитной памяти металла // Заводская лаборатория, 2008, № 3. С.42-47.
7. Дубов А.А. Исследование процесса усталостного разрушения стальных образцов с использованием метода магнитной памяти металла // Территория NDT, 2016, № 3. С.40-43.
8. Дубов А.А., Дубов Ал.А. Опыт применения бесконтактной магнитометрической диагностики трубопроводов и перспективы ее развития // Контроль. Диагностика, 2015, №10. С.21-24.